Frequent Questions for Regulated Stakeholders about Implementing the Formaldehyde Standards for Composite Wood Products Act
The following frequently asked questions (FAQs) address concerns regulated stakeholders may raise regarding implementation of the Formaldehyde Emission Standards for Composite Wood Products final rule pursuant to Title VI of the Toxic Substances Control Act (TSCA).
- Read more about the Formaldehyde Emission Standards for Composite Wood Products final rule.
- View or download this information in PDF format.
FAQs are sorted into the following topics:
- Applicable Products
- Accreditation Bodies
- Third-Party Certifiers
- Annual Reports
- Agent for Service
- Laminated Products
- Testing and Certification
- No-Added Formaldehyde-Based (NAF) and Ultra Low-Emitting Formaldehyde (ULEF) Resins
- Recordkeeping and Reporting
- Labeling
- Importing
- Stockpiling
- Secondhand Goods
- Starting-Up New Mills
- Use of Experimental Product and Resin Systems
- Suspension and/or Revocation of a Third-Party Certifier's EPA Recognition
- Miscellaneous
Applicable Products
1. What are the specific composite wood products covered by the final rule and the emission limits for each product type?
Under Title VI of the Toxic Substances Control Act (TSCA), three composite wood products are regulated: hardwood plywood, medium-density fiberboard (MDF, including thin-MDF), and particleboard.
Hardwood plywood is defined as a hardwood or decorative panel that is intended for interior use and composed of (as determined under ANSI/HPVA HP-1-2016) an assembly of layers or plies of veneer, joined by adhesive with a lumber core, a particleboard core, a medium-density fiberboard core, a hardboard core, a veneer core, or any other special core or special back material. Hardwood plywood includes laminated products except as provided at 40 CFR 770.4 (see the Laminated Products portion of the Q&A page for more info). The emission standards for hardwood plywood only apply to hardwood plywood made with a veneer core or a composite core. A composite core consists of a combination of layers of veneer and particleboard or medium-density fiberboard.
Medium-density fiberboard is defined as a panel composed of cellulosic fibers made by dry forming and pressing a resonated fiber mat (as determined under ANSI A208.2-2016). This includes thin-MDF, which has a thickness less than or equal to 8 millimeters or 0.315 inches.
Particleboard is defined as a panel composed of cellulosic material in the form of discrete particles (as distinguished from fibers, flakes, or strands) that are pressed together with resin (as determined under ANSI A208.1-2016).
Product Type | Emission Limits |
---|---|
Hardwood plywood | 0.05 ppm |
Medium-density fiberboard | 0.11 ppm |
Thin medium-density fiberboard | 0.13 ppm |
Particleboard | 0.09 ppm |
There are limited testing and certification exemptions for no-added formaldehyde-based (NAF) resins or ultra-low emitting formaldehyde (ULEF) resins.
2. What specific products are not covered by the final rule?
The following products are not covered by regulation:
- Hardboard;
- Structural plywood (per PS-1 standard);
- Structural panels (per PS-2 standard);
- Structural composite lumber (per ASTM D5456 standard);
- Military-specified plywood;
- Curved plywood (see Is “curved plywood” regulated by the TSCA Title VI final rule? in this section for more information);
- Oriented strand board;
- Prefabricated wood I-joists (per ASTM D5055 standard);
- Finger-jointed lumber;
- Wood packaging, such as pallets, crates, spools, and/or dunnage (this exempts wood packaging from the TSCA Title VI emission standards even if the wood packaging might otherwise, in the absence of the exemption, be regulated);
- Composite wood products used inside a new vehicle other than a recreational vehicle [Note: Mobile homes and/or trailer homes are considered manufactured housing and are regulated under TSCA Title VI];
- Composite wood products used inside new rail cars, boats, aerospace craft, or aircraft;
- Windows that contain composite wood products, if the windows contain less than 5% composite wood product by volume; and
- Exterior doors and garage doors that contain composite wood products, if the doors are made from composite wood products manufactured with NAF or ULEF resins, or the doors contain less than 3% composite wood product by volume.
3. Is “curved plywood” regulated by the TSCA Title VI final rule?
Curved plywood (including bent plywood) is exempt from the definition of hardwood plywood under TSCA Title VI. EPA further notes that this is consistent with the California Air Resources Board’s (CARB’s) current approach to management of curved and bent plywood under the Air Toxics Control Measure (ATCM) standards.
4. Are molded products, such as toilet seats, subject to the final rule?
If these products are fabricated using regulated composite wood panels, then they are regulated under the final rule either as a component part (if they are used in the construction or assembly of finished goods) or as a finished good. However, if these products are not fabricated from panels and are compression molded, or otherwise individually pressed in a way that does not involve the use of a regulated composite wood panel, then they are not subject to the final rule.
5. I manufacture a specialty panel. Am I regulated under the final rule?
To determine if you are regulated, confirm whether you are manufacturing a composite wood panel that meets the definitions for either hardwood plywood, medium density fiberboard, or particleboard as outlined in the respective voluntary consensus standards (e.g., ANSI, ASTM) incorporated in the final rule. In some instances, industry terms and product marketing designations give the appearance that a product is unregulated, but the product qualifies as a regulated composite wood product as per the definition(s) with the incorporated voluntary consensus standard. For example, medium density fiberboard may be marketed as “high-density fiberboard,” in some applications. The final rule states that if a panel meets the applicable voluntary consensus standard definition(s) in its construction, then it is regulated under the final rule.
6. I manufacture, import, distribute, retail, or sell a product that does not meet the definition of any regulated composite wood products (i.e., HWPW-VC, HWPW-CC, PB, MDF, or thin-MDF), but does meets the construction requirements specified in the relevant voluntary consensus standard of one of the excepted products listed under 40 CFR 770.1(c). What responsibility do I have under the final rule?
40 CFR 770.1(c) of the rule lists products (with their relevant standards, where applicable) that are excluded from regulation. The Agency believes that panel producers are best able to make the initial determination of whether the specific product(s) they produce meet the definition of one of the excluded products at 40 CFR 770.1(c). If a manufacturer, importer, distributor or retailer of a product believes the product does not meet the definition of any regulated composite wood products (or any applicable downstream entity), then they should be prepared to demonstrate to the Agency any claim that a product is excluded from TSCA Title VI regulation because it fits into one of the excluded categories provided in 40 CFR 770.1(c). As an example, a product may meet a claimed exclusion if it was manufactured according to the requirements or standards of one of the excluded products at 40 CFR 770.1(c), even if that product failed to meet the regulatory exclusion requirements. If there is information (such as engineering, construction, or laboratory analysis) documenting an attempt to meet the exclusion requirement of the select product at 40 CFR 770.1(c), that may nonetheless be sufficient to justify to the Agency the manufacturer’s exclusion claim under 40 CFR 770.1(c).
7. I manufacture a product that was constructed in accordance with PS-1-09 or PS-2-10 and then tested by a certifier authorized to certify those products, but the product failed to achieve certification due to a performance or construction characteristic under the PS-1-09 or PS-2-10 standard. Are these products, which were manufactured using a phenol-formaldehyde resin and constructed according to and tested to the PS-1-09 or PS-2-10 standards, subject to the formaldehyde emission standards for hardwood plywood since they are unable to be stamped as certified to the PS-1-09 and PS-2-10 structural standards?
No. Manufacturers of PS-1-09 or PS-2-10 panels that failed to achieve full certification due to a construction or performance failure that would not result in increased formaldehyde emissions, but which were manufactured according to and tested by a qualified certifier of PS-1-09 or PS-2-10 panels, would not be required to test and certify these panels as hardwood plywood under the TSCA Title VI regulation. A manufacturer, importer, distributor or retailer of these PS-1-09 or PS-2-10 “downfall” products must provide proof, upon request by the Agency, that their product is excluded from the regulation because it was constructed in accordance with the PS-1-09 or PS-2-10 standards. EPA believes that a laboratory report noting the construction or performance deficiency from the certifier, or a comparable document from the certifier stating that the panels were manufactured in accordance with but failed to meet the PS-1-09 or PS-2-10 standard (which would result in not obtaining a PS-1-09 or PS-2-10 product standard stamp of certification) would be the types of documents the manufacturer should be prepared to provide the Agency.
8. PS-1-09 and PS-2-10 are U.S. standards for structural plywood. Other countries have slightly different standards. Will panels that meet structural plywood standards (such as the European or Australian standards for structural plywood) be accepted by the EPA as equivalent to PS-1-09 and PS-2-10?
No. The TSCA Title VI regulation only recognizes standards listed under 40 CFR 770.1(c) and products made to those standards as being excluded from the TSCA Title VI regulation.
9. Who is subject to the final rule requirements?
All entities along the supply chain, from the manufacture to the sale of composite wood products, are affected by the final rule requirements. This includes panel producers, fabricators, third-party certifiers, importers, distributors, retailers, and accreditation bodies. If you are unsure if your business fits into one of these categories, examples of each include (but are not limited to):
Importers, distributors, and retailers
- Furniture stores or merchant wholesalers.
- Lumber, plywood, millwork, and wood panel merchant wholesalers.
- Building material and supplies dealers.
- Manufactured (mobile) home dealers (also includes trailer homes)
- Recreational vehicle dealers and merchant wholesalers.
- Other construction material merchant wholesalers, or wholesale distributors of manufactured homes and/or prefabricated buildings.
Panel producers
- Veneer product manufacturing
- Plywood product manufacturing
- Engineered wood product manufacturing
Fabricators
- Manufactured (mobile) home manufacturing
- Prefabricated wood building manufacturing
- Motor home and recreational vehicle manufacturing
- Travel trailer and camper home manufacturing
- Furniture and related product manufacturing
Third-Party Certifiers (TPCs)
- Laboratories conducting independent third-party formaldehyde emissions testing of regulated composite wood products
Accreditation Bodies (ABs)
- Product ABs
- Laboratory ABs
10. I am a renovator/contractor who installs composite wood products in new or existing houses on-site at real property. Are there any requirements that apply to me under the TSCA Title VI regulation beginning June 1, 2018?
Renovators (e.g., contractors or handymen) who install composite wood products or finished goods (purchased either by the property owner or by the renovator on behalf of the property owner as part of materials for the project) in buildings or other structures that are constructed on site and become a permanent addition to real property are neither fabricating those finished goods to be sold nor retailing those composite wood products or finished goods. Renovators who are not affiliated with a brand of product or supplier are not considered fabricators or retailers under the TSCA Title VI final rule.
TSCA Title VI regulations apply to any renovator who is also a retailer selling composite wood products or finished goods directly to consumers (e.g., direct purchase stores for consumers) and who also happens to install, or provide installation services after purchase, including through subcontractors. Subcontracted renovators who provide services to real property on the behalf of retailers, but do not directly sell composite wood products or finished goods to consumers, are not regulated as retailers under the TSCA Title VI final rule.
For example: a contractor or renovator may have responsibilities under the TSCA Title VI final rule if that renovator or contractor is a custom cabinetmaker. If the custom cabinetmaker is making finished goods from composite wood products or component parts and then selling the finished goods either to a retailer or the public, that contractor or renovator could be a fabricator, distributor, retailer, or a combination of all three.
11. Is there a de minimis amount of composite wood that would not be subject to the regulations?
No. Finished goods, including component parts sold separately to end users, containing only a de minimis amount of regulated composite wood product are exempted from only the labeling requirements. However, the underlying composite wood core material contained within a finished good must still meet the applicable emission standard and be tested and certified. A finished good, including component parts sold directly to consumers, contains a de minimis amount of regulated composite wood product if its regulated composite wood product content does not exceed 144 square inches, based on the aggregate sum of each regulated composite wood product’s largest surface faces within the component part or finished good. The exception does not apply to finished goods or component parts designed to be used in combination or in multiples to create larger surfaces, finished goods, or component parts.
12. Lumber core products are not subject to the CARB Airborne Toxic Control Measures (ATCM) to Control Formaldehyde Emissions from Composite Wood Products. Are they subject to EPA’s final rule?
No. The definition of hardwood plywood in the final rule includes a variety of core types, but formaldehyde emission standards only apply to hardwood plywood made with a veneer core or a composite core. Hardwood plywood made with a lumber core or a hardboard core is not required to comply with the emission standards or the testing and certification provisions.
13. Is structural plywood regulated under the final rule?
No. The definition of hardwood plywood in the final rule does not include structural plywood as defined in the voluntary consensus standards incorporated into the rule at 40 CFR 770.1(c). Many of the product exemptions under the final rule, such as hardboard, oriented strand board, structural plywood, structural panels, and structural composite lumber, were found to already be made with resins with reduced formaldehyde emissions.
14. Is bamboo covered under TSCA Title VI?
To the extent that bamboo is used in the production of a composite wood product that meets the voluntary consensus standards for medium-density fiberboard or particleboard, it is covered by the regulation. With respect to hardwood plywood, to the extent that bamboo is used to make a product that fits within the statutory definition or the voluntary consensus standard, and the product can be characterized as being made with a veneer core or a composite core, the product is covered by the regulation. So, for example, a product made by affixing a bamboo veneer to a particleboard, medium-density fiberboard, or a veneer core would be either hardwood plywood that must be certified or a laminated product and subject to the laminated product provisions.
Accreditation Bodies
1. When do the final rule requirements come into force for ABs?
The formaldehyde emission standards came into force beginning June 1, 2018. ABs wishing to participate in the EPA Toxic Substances Control Act (TSCA) Title VI Third-Party Certification Program (EPA Program) could begin applying to EPA for recognition beginning on May 22, 2017.
The regulations require that all EPA TSCA Title VI Third-Party Certifiers (TPC) (except those that are California Air Resource Board (CARB) approved and entering under the reciprocity provisions at 40 CFR 770.7(d)) must be accredited by an AB to ISO/IEC 17065:2012(E) and be a TPC, or contract with a laboratory that is accredited to ISO/IEC 17025:2005(E) with scopes of accreditation to include “40 CFR Part 770 – Formaldehyde Standards for Composite Wood Products” before entering the program. For TPCs that enter the TSCA Title VI program as CARB-approved TPCs under the reciprocity provisions at 40 CFR 770.7(d), they will have to gain both accreditations with an EPA TSCA Title VI AB by the end of the transitional period (i.e., March 22, 2019) to continue to certify composite wood products under TSCA Title VI. See frequent questions for TPCs.
2. I am a product and/or laboratory AB. How do I obtain EPA recognition under the EPA program?
To become recognized as an EPA TSCA Title VI AB, you must apply to EPA using the EPA Central Data Exchange (CDX).
The application requirements for product and laboratory ABs are available under 40 CFR 770.7(a)(2) and (b)(2), respectively. ABs may choose to apply to be recognized as one or both types of ABs (product or laboratory only, or product and laboratory AB). The CDX online application will allow you to select either one or both AB types and provide the information required in the sections.
3. What is the application fee for ABs to enter into a recognition agreement with EPA to become an EPA TSCA Title VI AB?
EPA does not charge fees for ABs to be recognized as an EPA TSCA Title VI AB or when ABs renew their applications.
4. How long are ABs recognized under the EPA program?
EPA TSCA Title VI ABs are recognized for three years from the date of approval into the program, so long as they maintain good standing in the TSCA Title VI Third Party Certification Program. ABs interested in being recognized under the EPA Program must enter into a recognition agreement with EPA. To maintain their recognition for another three years, an EPA TSCA Title VI AB must submit a renewal application to EPA before the three-year period of their recognition agreement lapses. If an EPA TSCA Title VI AB fails to apply for renewal prior to the expiration of the previous recognition agreement, then its recognition will lapse, and the EPA TSCA Title VI AB may not provide accreditation services under TSCA Title VI.
5. How do I renew my recognition agreement?
Once a recognition agreement is established between EPA and an AB, the AB must submit an application for renewal to EPA via CDX before the end of the three-year recognition period if the AB wishes to renew the recognition agreement. The application must indicate any changes from the AB’s initial application or most recent renewal application.
Third-Party Certifiers
1. When do the final rule requirements come into force for TPCs?
The formaldehyde emission standards came into force beginning June 1, 2018. All TPCs (including California Air Resources Board (CARB) approved TPCs) must be recognized by EPA prior to certifying any composite wood products under Title VI of the Toxic Substances Control Act (TSCA). TPCs could begin applying for EPA recognition as of May 22, 2017. Under the rule’s reciprocity provisions, CARB-approved TPCs will have a transition period, which will end March 22, 2019, to meet the accreditation requirements under the final rule. During the transition period, CARB-approved TPCs must comply with all other aspects of the final rule. Non-CARB-approved TPCs may apply to EPA to become recognized under the EPA TSCA Title VI Third-Party Certification Program (EPA Program) to certify composite wood products only after their Accreditation Body (AB) is recognized by EPA and TPCs are properly accredited by that AB.
2. I am a non-CARB TPC. How do I obtain EPA recognition under the final rule?
To become recognized as an EPA TSCA Title VI TPC, you must apply via the EPA Central Data Exchange (CDX). A non-CARB TPC may apply only after their AB is recognized by EPA and the TPC is properly accredited by their AB.
3. I am a CARB-approved TPC. How can I apply for EPA recognition through CDX if I do not have an EPA TSCA Title VI AB?
CARB-approved TPCs will have a transition period, which ends on March 22, 2019, to be accredited to the required standards under the final rule by an EPA TSCA Title VI AB. During this transition period, CDX will allow CARB-approved TPCs to bypass the selection of an EPA TSCA Title VI AB during the application process. By March 22, 2019, to continue to certify composite wood products under TSCA Title VI, CARB-approved TPCs must meet all accreditation requirements outlined in the final rule and amend their CDX application to identify their EPA TSCA Title VI AB.
4. How do I know if an AB is recognized by EPA?
A list of recognized ABs can be found online.
5. How long are TPCs recognized under the EPA program?
EPA TSCA Title VI TPCs are recognized for two years. To maintain their recognition, EPA TSCA Title VI TPCs must submit a renewal application to EPA every two years. They must also have a reassessment or surveillance on-site assessment conducted by their EPA TSCA Title VI AB every two years.
6. How do I renew my recognition as an EPA TSCA Title VI TPC?
TPCs must submit a renewal application renewal to EPA via CDX. This renewal application should be submitted before the two-year period of recognition ends to ensure continued coverage. The application must indicate any changes from the TPC’s initial application or most recent renewal application.
7. Will current CARB TPC identification numbers be utilized under the EPA Program?
To align with the current CARB program, CARB-approved TPCs recognized by EPA through reciprocity will retain their current CARB TPC identification number. EPA created this provision to prevent unnecessary recordkeeping, reporting, and identification issues in tracking products certified by current CARB-approved TPCs. For non-CARB TPCs that receive EPA recognition under TSCA Title VI, EPA will issue numbers that follow a format like the CARB-approved TPC numbers to maintain consistency for users and panel producers in recordkeeping and inventory control.
8. Are TPCs recognized under the EPA program required to participate in CARB interlaboratory comparisons when they are offered by CARB?
To align with the current CARB program, all EPA TSCA Title VI laboratories or contract laboratories (defined as a “TPC laboratory” in the final rule) must participate in the CARB interlaboratory comparison for formaldehyde emissions, when offered. This includes TPC laboratories of both CARB-approved TPCs and non-CARB TPCs. CARB intends to conduct the interlaboratory comparisons no less frequently than every two years. EPA determined that requiring participation in the CARB interlaboratory comparison on a regular basis is necessary to verify that TPC laboratories under the final rule can properly measure formaldehyde emissions from composite wood products.
9. In the event of unsafe conditions in the geographic area that would prevent a third-party certifier (TPC) from traveling in-person to that area, how can a TPC work with a new or existing TSCA Title VI-certified composite wood product manufacturing panel producer to conduct initial, onsite inspections and/or quarterly inspections (including sampling collections of composite wood products) to ensure TSCA Title VI compliance until the unsafe conditions are no longer present?
In the event a government entity has identified the existence of unsafe conditions (e.g., natural disasters, outbreaks, political unrest, epidemics, and pandemics) in the area of a composite wood product manufacturing panel producer that would prevent the required quarterly inspections from being conducted in-person onsite, a TPC may opt to perform a remote quarterly inspection in lieu of the in-person onsite inspection. Such a remote inspection may occur only during the period of the unsafe conditions identified by a government entity. For such a remote inspection during the period of the unsafe conditions, the TPC must conduct a remote quarterly inspection via live remote technology (e.g., video/teleconference) operating as directed by the TPC to satisfy the requirements of 40 CFR 770.7(c)(4)(i)(F), and work with the panel producer quality control manager at that time to select, package, sign, and ship the TPC panels/samples for the quarterly test according to 40 CFR 770.20(c). TPCs and panel producers must remain in close communication with each other to ensure any changes or developments that might affect the panel producer or product type certification are managed according to the TSCA Title VI regulations. The panel producer and TPC should also document each occurrence of unsafe conditions for auditing purposes, and the TPC must notify EPA through the Annual Report submission process indicating that a remote inspection has occurred. The standard practice for a TPC providing certification services for composite wood panel producers remains that a TPC conducts in-person quarterly inspections and sample collection, packaging, signature, and shipping for quality control testing, which should resume as soon as possible when the unsafe conditions end.
In the event a government entity has identified the existence of unsafe conditions as outlined above, in order to conduct the required initial, onsite inspection associated with new certification activities, the TPC may conduct a virtual inspection via onsite video/teleconference technology (operating as directed by the TPC) and that aligns with the standard operating procedure the TPC would normally employ during an in-person inspection to satisfy the requirements of 40 CFR 770.15(c)(1)(viii). The standard practice for a TPC providing certification services for composite wood panel producers remains that a TPC conducts initial (in-person) onsite inspections, which should resume as soon as possible when the unsafe conditions end.
Annual Reports
1. What timespan must the Accreditation Body (AB) and Third-Party Certifier (TPC) annual reports cover?
Annual reports must be submitted no later than March 1 of each year starting March 1, 2018, and the report must cover the previous calendar year in which TSCA Title VI accreditation or certification activities were conducted. For example, the 2017 annual report from each AB or TPC that is submitted by March 1, 2018, will contain information and data required under the TSCA Title VI for services provided from January 1, 2017 through December 31, 2017. The annual report for the prior year may be submitted at any time after January 1 but no later than March 1 of each year.
2. How should I submit my annual report to EPA?
Annual reports must be submitted to EPA electronically through the Central Data Exchange (CDX). CDX is the same system ABs and TPCs used to apply for EPA recognition to participate in the TSCA Title VI program. Access CDX online. EPA will not accept reports by email or paper versions submitted by mail. Note that these annual reports can be shared automatically with CARB through the CDX system for those TPCs that also have reporting responsibilities under CARB.
3. Am I required to submit an annual report for years that I have not conducted any activities under the TSCA Title VI program?
If during the calendar year the AB or TPC does not perform any services for accreditation or certification of products under TSCA Title VI, then no annual report would be required.
Agent for Service
1. What is an agent for service?
As defined in 40 CFR 770.3 of the final rule, an agent for service is an entity designated by a third-party certifier (TPC) or accreditation body (AB) to receive legal documents and communicate with EPA on their behalf. This is a requirement only for TPCs and ABs located outside of the United States. An agent for service must be a person or entity with a physical address in the United States and may be a company, firm, or other entity specializing in this role. The final rule permits TPCs and ABs to share an Agent for Service, meaning that multiple regulated entities may hire the same firm or company to accept documents on their behalf.
2. Is there any guidance EPA can provide on selecting an agent for service?
Many private import brokers located in the United States provide import agent services. Whomever you choose, the agent for service must be able to accept notices and processes made in administrative and judicial proceedings. Your agent for service must have a physical address within the United States, maintain regular business hours to receive notices and documents, forward all legal paperwork and correspondence to your business, and maintain copies of your company’s files, as specified. Agents for service are available in every state in the United States.
3. Is an agent for service required during the transitional period for CARB-approved TPCs that are located outside of the United States?
Yes. CARB-approved TPCs located outside of the United States must have an agent for service during the transition period and must provide this information in their application.
Laminated Products
1. What are considered laminated products and are they required to be tested for formaldehyde emissions? If so, by when?
A laminated product is a product in which a wood or woody grass veneer is affixed to a regulated particleboard core or platform, a medium-density fiberboard core or platform, or a veneer core or platform. A laminated product is a component part used in the construction or assembly of a finished good. In addition, a laminated product is produced by either the fabricator of the finished good in which the product is incorporated or a fabricator who uses the laminated product in the further construction or assembly of a component part.
Beginning March 22, 2024, laminated product producers whose products are not exempted from the definition of hardwood plywood will be included as producers of hardwood plywood and will be required to test and certify their products to ensure they comply with the formaldehyde emission standard for hardwood plywood.
2.What are the requirements for a laminated product producer?
Laminated product producers are also fabricators and, beginning June 1, 2018, all laminated product producers must comply with the rule requirements for fabricators. As fabricators, laminated product producers are required to take reasonable precautions for compliance, maintain records, and label finished goods that contain regulated composite wood products accordingly.
Beginning March 22, 2024, producers of laminated products not exempt from the definition of “hardwood plywood” will also become regulated as hardwood plywood producers, and will be responsible for the same testing, certification, recordkeeping, and labeling as a panel producer of hardwood plywood.
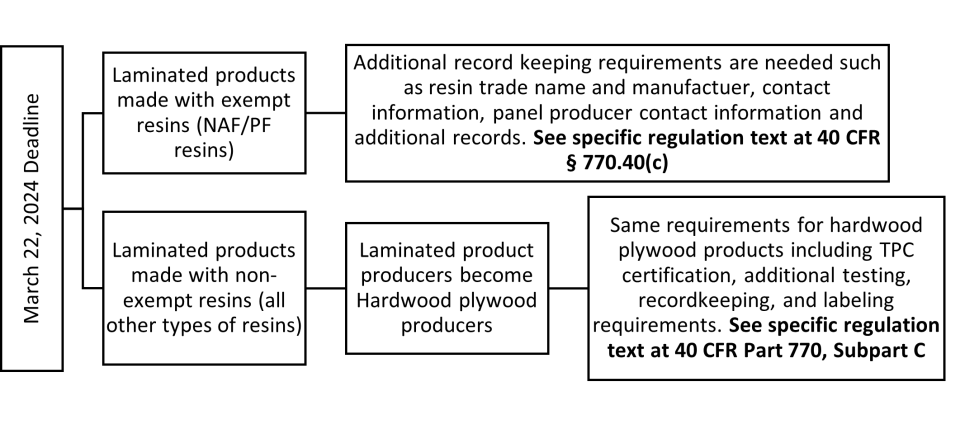
3. What are the rule requirements for a producer of an exempt laminated product?
Laminated product producers are also fabricators and, beginning June 1, 2018, must comply with the rule requirement for fabricators. As fabricators, laminated product producers are required to take reasonable precautions for compliance, maintain records, and label finished goods that contain regulated composite wood products accordingly.
Beginning March 22, 2024, producers of a laminated product will no longer be exempt under 40 CFR 770.4 from the definition of “hardwood plywood.” They will be required to begin complying with the recordkeeping requirements at 40 CFR 770.40(c). These records demonstrate the laminated product producer’s eligibility for the exemption from the rule requirements applicable to hardwood plywood producers (such as testing and certification).
4. I am a laminated product producer who wants to use a resin that does not fall under the no-added formaldehyde (NAF) or phenol formaldehyde (PF) exemption. Am I allowed to use an alternate resin?
Yes. However, beginning March 22, 2024, any laminated product made with a resin that is not a PF or NAF resin (or resin otherwise approved through the resin petition process at 40 CFR 770.4) will be considered a “non-exempt” laminated product and you will be a HWPW producer and must comply with all the requirements of a HWPW panel producer, including testing and certification of the product as HWPW, as well as associated recordkeeping documents required of a panel producer.
5. Can I petition EPA to expand the exemptions from HWPW for additional resins used to produce a laminated product?
Yes. The petition process is outlined in 40 CFR 770.4.
6. What are the requirements for laminated products that are manufactured (including imported) prior to March 22, 2024 and are still in inventory (stores or distribution center) in the U.S. on and after March 22, 2024? Are they subject to third-party certification and required to meet the HWPW emissions standard or otherwise be exempted under 40 CFR 770.4(a)?
Laminated products manufactured (including imported) on or before March 21, 2024 may be used to fabricate component parts or finished goods at any time and are not subject to third-party certification and testing to meet the hardwood plywood emission standard or otherwise be exempted under 40 CFR 770.4(a). EPA established the compliance date for laminated products as a manufactured-by date. In 2017, EPA clarified this by rulemaking (see 82 FR 44533 at page 44535). Fabricators who use laminated products, among other regulated entities, must continue to take reasonable precautions to ensure compliance per 40 CFR 770.30.
7. What are the emission standards for laminated products beginning March 2024?
Beginning March 22, 2024, laminated products will be considered hardwood plywood and must meet the emission standards for hardwood plywood of 0.05 ppm unless exempted under 40 CFR 770.4(a).
8. What is a component part under laminated products?
Component part means an object other than a panel that contains one or more composite wood products and is used in the construction or assembly of finished goods. Component parts that are sold directly to consumers are considered finished goods.
9. Is corkboard included in the definition of a woody or woody grass veneer?
Cork is not considered a woody or woody grass veneer under the TSCA Title VI regulations (which incorporate HP-1) and therefore would not be an applicable laminated product.
10. What is the difference between an importer, fabricator, laminated product producer, panel producer, distributor, and retailer?
Distributor | Distributor means any person or entity to whom a composite wood product, component part, or finished good is sold or supplied for the purposes of resale or distribution in commerce, except that manufacturers and retailers are not distributors. |
Fabricator | Fabricator means a person or entity who incorporates composite wood products into component parts or into finished goods. This includes laminated product producers, but persons or entities in the construction trades are not fabricators by renovating or remodeling buildings. |
Importer |
Importer means any person or entity who imports composite wood products, component parts, or finished goods into the customs territory of the United States (as defined in general note 2 of the Harmonized Tariff Schedules of the United States pursuant to 15 U.S.C. 2612(a)(1)). Importer includes: (1) The entity primarily liable for the payment of any duties on the products; or (2) An authorized agent acting on the entity's behalf. |
Laminated Product Producer | Laminated product producer means a manufacturing plant or other facility that manufactures (excluding facilities that solely import products) laminated products on the premises. Laminated product producers are fabricators and, beginning March 22, 2024, laminated product producers are also hardwood plywood panel producers except as provided at 40 CFR 770.4. |
Panel Producer | Panel producer means a manufacturing plant or other facility that manufactures (excluding facilities that solely import products) composite wood products on the premises. |
Retailer | Retailer means any person or entity that sells, offers for sale, or supplies directly to consumers composite wood products, component parts or finished goods that contain composite wood products, except that persons or entities in the construction trades are not considered retailers by selling, renovating, or remodeling buildings. |
11. Do laminated products need to include a label?
Fabricators of finished goods containing laminated products must comply with the rule requirements for fabricators. As fabricators, requirements for laminated product producers include taking reasonable precautions for compliance (40 CFR 770.30), maintaining records (40 CFR 770.40(d)), and labeling finished goods that contain regulated composite wood products accordingly (40 CFR 770.45). Beginning March 22, 2024, laminated products are considered hardwood plywood and must follow the same requirements as a panel producer under 40 CFR Part 770, Subpart C, which for labeling means that laminated products that are imported, sold, supplied, or offered for sale to a fabricator for further fabrication must be labeled as hardwood plywood would be. Each finished good or every box or bundle containing finished goods must be labeled.
12. I am a fabricator of component parts or finished goods who either manufacturers in-house or purchases TSCA Title VI-compliant HWPW, MDF, or PB panels from a qualified panel producer. I provide these composite wood panels, or smaller cut pieces, to a separate entity who then adheres wood or woody grass veneers to the face and back of each panel or piece on a subcontract basis. The separate entity then delivers the veneer-laminated panels or pieces back to me for my use to produce a component part or finished good. Is the separate entity providing veneer lamination services classified as a panel producer or a laminated product producer?
Entities that adhere wood or woody grass veneers to the face and back of a TSCA Title VI-compliant composite wood panel (or smaller cut pieces thereof), whether or not on a subcontract basis, and then deliver these veneer-laminated panels or pieces to a fabricator or other customer without first additionally fabricating the veneered materials into a component part or finished good are not laminated product producers; rather, they are hardwood plywood panel producers. The third-party certification or NAF/ULEF exemption requirements applicable to composite wood panels described in 40 CFR Part 770 Subpart C apply. Entities that do not produce laminated products are not eligible to claim the exemptions from the definition of hardwood plywood for certain laminated products as provided in 40 CFR 770.4(a).
This is because EPA’s definition of the term “laminated product” provided in 40 CFR 770.3 limits applicability to products made by fabricators of the finished goods in which the laminated product is incorporated, or to products made by fabricators who use the laminated products in the further construction or assembly of component parts. EPA’s definition of the term “panel” specifies that the simple act of “[c]utting a panel into smaller pieces, without additional fabrication, does not make the panel into a component part or finished good.”
13. If a composite wood product is made by adhering a wood or woody grass veneer to one side of a TSCA Title VI-compliant HWPW, MDF, or PB platform using a formaldehyde containing resin, is this product type required to be tested and certified according to the provisions for laminated products provided in 40 CFR 770.2 (e)(2)?
Assuming the product is “a component part used in the construction or assembly of a finished good” and “produced by either the fabricator of the finished good in which the product is incorporated or a fabricator who uses the laminated product in the further construction or assembly of a component part” (per the definition of laminated product under 40 CFR 770.3), a wood or woody grass veneer adhered to one or both sides of a regulated HWPW, MDF, or PB core or platform is considered a laminated product and, beginning March 22, 2024, must comply with the requirements of hardwood plywood producers under 40 CFR Part 770, Subpart C.
Laminated products made using a phenol-formaldehyde (PF) resin or resins formulated with no-added formaldehyde (NAF) as part of the resin cross-linking structure are considered exempt from the definition of hardwood plywood, as provided in 40 CFR 770.4(a). Beginning March 22, 2024, producers of laminated products who wish to take advantage of the exemption for laminated products made using either a NAF or PF resin are required to retain records as described under 40 CFR 770.40(c) in addition to the existing record-keeping requirements for fabricators described under 40 CFR 770.30.
14. If a laminated product is made by adhering a wood or woody grass veneer to one side of a TSCA Title VI-compliant MDF or PB platform using a formaldehyde-containing resin, how should samples of this product type be prepared for the purposes of testing using either the primary ASTM E1333 or secondary ASTM D6007 test methods?
Beginning March 22, 2024, unless excluded as provided in 40 CFR 770.4(a), laminated products made by adhering a wood or woody grass veneer to one side of a TSCA Title VI-compliant composite wood core or platform must be tested and certified as conforming to the TSCA Title VI emission standards for hardwood plywood. ASTM E1333 and the ASTM D6007 test methods describe certain test specimen preparation procedures for non-standard sample configuration testing for products with a single surface exposed. For certain laminated products in which a wood or woody grass veneer is adhered to one side of a TSCA Title VI compliant MDF or PB core or platform then, as described in both ASTM E1333 and ASTM D6007 test methods, two pieces can be tested back-to-back with the edges taped together to make one test specimen. The formaldehyde emissions thus would only be measured from the side that is veneered. As specified in ASTM E1333 and ASTM D6007, test reports issued by the test laboratory should identify the samples as having been tested in the back-to-back mode.
15. I am an integrated producer of composite wood panels, component parts, and finished goods who produces both composite wood panels and laminated products in separate production steps/phases. Am I required to separately test and certify both the composite wood panels and laminated products or can they be certified as one?
Prior to March 22, 2024, laminated product producers must have tested and certified, or sourced TSCA Title VI compliant composite wood panels to be used as the core or platform for their laminated products. Beginning March 22, 2024, laminated products must be tested and certified as conforming to the emission standards for hardwood plywood unless excluded based on the use of no-added formaldehyde (NAF) or phenolic resins as provided in 40 CFR 770.4(a). This also results in producers of non-exempt laminated products becoming designated as a panel producer under 40 CFR Part 770, Subpart C beginning March 22, 2024.
From March 22, 2019, fabricators who sourced composite wood panels from outside their manufacturing process to make a laminated composite wood product are required to utilize TSCA Title VI compliant composite wood panels. Beginning March 22, 2024, fabricators of component parts and finished goods are still required to source and utilize TSCA Title VI compliant composite wood panels. If the fabricator laminates a wood or woody grass veneer to one or both sides of a TSCA Title VI compliant composite wood panel using a resin that contains formaldehyde, then the fabricator will also be required to test and certify those laminated products as hardwood plywood. Therefore, beginning March 22, 2024, both the composite wood panel and the non-exempt laminated composite wood product need to be tested and certified under the final rule (unless both the composite wood panel and laminated product are made in-house (see Question 16 below)). Fabricators of non-exempt laminated products are also required to retain records and labels as a panel producer.
16. For entities that test and certify both composite wood panels and laminated products, what are some considerations to be made aware of?
For producers of hardwood plywood panels and laminated products consisting of a regulated composite wood core or platform that is made in-house, the regulated core or platform does not have to be certified independently but can be tested and certified as part of the hardwood plywood/laminated product certification. If a producer of laminated products wishes to take advantage of the exemption for laminated products made with phenol-formaldehyde resins or resins formulated with no-added formaldehyde as part of the resin cross-linking structure, then the producer must use a certified core or platform, whether purchased or made in-house.
Producers of 2-ply laminated products (wood or woody grass veneer adhered to one side of an MDF or PB core or platform) must always use a certified MDF or PB core or platform, whether purchased or made in-house. Unless the producer is eligible to take advantage of the exemption for laminated products made with phenol-formaldehyde resins or resins formulated with no-added formaldehyde as part of the resin cross-linking structure, the producer must also certify the 2-ply laminated product after the veneer is applied (0.05 ppm emission standard measured from the veneered face).
17. I am a producer of laminated products in which a regulated composite wood core or platform is first cut, profiled, or shaped into a non-flat surface. A wood or woody grass veneer is then adhered to one or both sides of this shaped or profiled core or platform using a resin that contains formaldehyde. Are these non-flat laminated products required to be tested and certified according to the provisions described in 40 CFR 770.15 and 770.20, respectively? How are samples of these products to be prepared and tested for the purposes of determining conformance to the emission standards for hardwood plywood?
EPA's definition of the term “laminated product” does not draw any distinction between the emission standards and requirements for laminated products that exhibit flat versus non-flat surfaces. Therefore, beginning March 22, 2024, a producer of laminated products consisting of a wood or woody grass veneer adhered to a composite wood core or platform that has been shaped or profiled to impart a non-flat surface must be tested and certified as conforming to the emission standards for hardwood plywood. Non-flat laminated products in which a wood or woody grass veneer is adhered to a shaped or profiled composite wood core or platform using either a phenol-formaldehyde resin or a resin formulated with no-added formaldehyde as part of the resin cross-linking structure are exempt from the definition of hardwood plywood as provided in 40 CFR 770.4(a).
Both ASTM E1333 and ASTM D6007 include provisions that explain that “[s]ome products such as kitchen and audio/video cabinets and wood furniture may be made using substantial quantities of wood product components containing formaldehyde. These products are not in flat panel form and are, from time to time, tested in large chambers to determine formaldehyde emission potential.” ASTM E1333 continues on to provide examples of how such products can be prepared for shipment for testing. Therefore, EPA determined that if testing cabinets and furniture is within the scope of the ASTM E1333 large chamber test method, the test method can also be used to test the emissions from laminated products that might not be flat. Similar provisions are made in the ASTM D6007 small chamber test method.
With regard to the requirements for test chamber loading ratios or Q/A ratios as provided in ASTM E1333 and ASTM D6007, EPA understands that irregular shapes may be a challenge, but it is possible to calculate surface areas. For channels or grooves that are difficult to accurately assess, both ASTM E1333 and ASTM D6007 allow for some flexibility in the estimation of the surface area used to calculate test chamber loading ratios or Q/A ratios for these irregularly shaped products. For laminated products exhibiting significant irregular surface shapes or profiles, the test laboratory should use its professional judgment to estimate the surface area as accurately as possible. As provided in the definition of “product type” in 40 CFR 770.3, composite wood products with similar emissions profiles may be grouped into a single product type for testing. Therefore, to minimize the test burden, producers of non-flat laminated products who choose to group products with varying shapes or surface profiles should test the product that is most likely to represent the “worst case” emissions performance. Samples of laminated products made by adhering a wood or woody grass veneer to one side of a certified MDF or Particleboard core or platform may be tested by placing two pieces back-to-back with the edges taped together to make one test specimen.
Testing and Certification
1. What composite wood products need to be tested and certified under the final rule?
Hardwood plywood (HWPW) (made with a veneer or composite core), medium density fiberboard (MDF, including thin-MDF), and particleboard panels need to be tested and certified. The final rule does not require the testing of component parts, finished goods, or articles containing regulated composite wood products after the initial testing of the composite wood panel used to fabricate the finished good or component part of a finished good. Beginning March 22, 2024, non-exempt laminated products will be designated as hardwood plywood and thus require testing and certification.
2. I am a fabricator. Do component parts or finished goods I fabricate need to be tested and certified under the final rule?
No. Beginning June 1, 2018, only composite wood products (i.e., panels) as defined under the final rule must undergo testing and meet emission standards certification requirements. Beginning June 1, 2018, fabricators and retailers are responsible for ensuring that they purchase only compliant composite wood products (i.e., panels that are certified) for use in the fabrication of component parts or finished goods. Also, if you are a fabricator that manufactures laminated products, beginning March 22, 2024, any non-exempt laminated products you fabricate will be required to be tested and certified as HWPW.
3. I am a panel producer who manufactures composite wood panels that are used in non-exempt laminated composite wood products. Beginning March 22, 2024, am I required to test both the composite wood panels and the non-exempt laminated composite wood products?
Beginning on March 22, 2024, a manufacturer of composite wood panels who uses those panels to fabricate a non-exempt laminated composite wood product will be required to test and certify the non-exempt laminated composite wood product that incorporates underlying composite wood panels. Prior to March 22, 2024, non-exempt laminated product producers must have tested and certified, or sourced, compliant composite wood panels to be integrated into the core of their laminated products. After March 22, 2024, the testing regimen shifts to the non-exempt laminated composite wood product being fabricated because that laminated product must now meet the HWPW emission standards. This also results in non-exempt laminated product producers becoming designated as a “panel producer” under the Toxic Substances Control Act (TSCA) Title VI final rule and must comply with the requirements of a panel producer.
From June 1, 2018 until March 22, 2019, if you are sourcing composite wood products from outside your manufacturing process to make a laminated composite wood product, the EPA requires that you only utilize CARB ATCM Phase II or TSCA Title VI compliant composite wood panels. From March 22, 2019, if you are sourcing composite wood panels from outside your manufacturing process to make a laminated composite wood product, the EPA requires that you only utilize TSCA Title VI compliant composite wood panels. After March 22, 2024, you will be required to test and certify your non-exempt laminated composite wood products as hardwood plywood through the EPA TSCA Title VI Third-Party Certification Program. After March 22, 2024, both the composite wood panel and the non-exempt laminated composite wood product need to be tested and certified under the final rule. You are also required to retain records and labels as a panel producer.
4. As a panel producer, I use the same resin to manufacture both HWPW veneer core panels and HWPW composite core panels. Because the resin is the same, is it possible to test both as one HWPW product type?
Yes. The definition of product type allows for groups of composite wood products, made by an individual panel producer and with the same resin system, that is different from another product type based on panel composition and formaldehyde emission characteristics, to be grouped together.
5. How do I know if the TPCs our suppliers use are both CARB approved and EPA-recognized?
You may confirm a TPC’s participation in the CARB program by consulting CARB’s website for a list of approved TPCs. This list also includes a field that notes if the TPC is recognized by EPA. Find an EPA recognized TPC.
6. Who is required to test formaldehyde emissions from composite wood products?
All panel producers are required to have their products tested by an EPA TSCA Title VI TPC (laboratories conducting independent third-party formaldehyde emissions testing of regulated composite wood products) to ensure their products are certified as compliant with the emissions standards. This includes a CARB-approved TPC that is recognized by EPA during the transition period. Panel producers are required to conduct quality control tests on a regular basis to ensure that regulated composite wood products meet emissions standards.
These tests can be conducted on-site if the appropriate equipment is available and test methods show a correlation to test method ASTM E1333-14 or, with a showing of equivalence, the test method ASTM D6007-14. They are also required to meet reporting and recordkeeping requirements for quality control. Beginning March 22, 2024, laminated product producers whose products are not exempted from the definition of hardwood plywood are also required to perform quality control tests on their products.
As part of the overall quality control system, TPCs are required to work with the panel producer to establish quality control limits (QCLs) for formaldehyde emissions for all product types, as well as determine a process to ensure panel producers (and laminated product producers) are meeting QCLs.
EPA TSCA Title VI TPCs or their laboratories must test their panel producers’ composite wood products quarterly using test method ASTM E1333–14 or, with a showing of equivalence, the test method ASTM D6007-14. On a quarterly basis, they must also inspect panel producers’ (and, if applicable, laminated product producers’) products and records and verify quality control test results.
7. Can a panel producer use a small emissions chamber (ASTM D6007-14) as a routine quality control test method?
Yes. Approved quality control test methods show a correlation to ASTM E1333-14, or the equivalent ASTM D6007-14 test method per 40 CFR 770.20(d). Other approved quality control test methods include:
- ASTM D5582-14;
- BS EN ISO 12460-3:2015 (Gas Analysis Method);
- DMC (Dynamic Micro Chamber), 2007 User’s Manual;
- DMC (Dynamic Micro Chamber), 2012 GP User’s Manual;
- BS EN ISO 12460-5:2015 (Perforator Method); and
- JIS A 1460:2015 (24-hr Desiccator Method).
8. Are fabricators or retailers of finished goods required to conduct formaldehyde emissions testing?
No. Formaldehyde emissions testing is required to be conducted by panel producers and their TPC. Fabricators and retailers are responsible for ensuring the purchase of only compliant composite wood products (i.e., panels) used in the fabrication of component parts or finished goods.
9. Do finished goods require testing and third-party certification?
No. Finished goods do not require formaldehyde emissions testing and certification. However, the finished good and component parts of the finished good must be fabricated with compliant composite wood panels. Fabricators are also required to keep records documenting the finished goods and components parts are made of compliant panels and fabricators must label the compliant finished goods or component parts as TSCA Title VI compliant.
10. What is a statement of compliance?
The final rule’s recordkeeping provisions include a requirement that all fabricators, importers, distributors, and retailers maintain invoices, bills of lading, or like documents that contain a statement of compliance with TSCA Title VI or a statement that the composite wood products were made before the designated date of manufacture. (Laminated product producers and importers also have other recordkeeping requirements.) A statement of compliance could be a short and simple statement on the face of the document affirming that the composite wood products in the shipment or order are compliant with TSCA Title VI. Copies of these invoices, bills of lading, or like documents showing the compliance statement have to be kept by fabricators, importers, distributors, and retailers for three years.
11. Does EPA provide any certificates?
No. EPA does not issue or provide any certificates. Certification is conducted by the EPA TSCA Title VI Third-Party Certifier (TPC) and a TPC may issue certificates to memorialize an approved application for third-party certification.
12. I am a producer of composite wood panels and non-exempt laminated products who is pursuing certification according to the EPA TSCA Title VI Third-Party Certification Program. Should I expect to receive separate certificates for the production of composite wood panels versus laminated products or is one certificate adequate?
40 CFR 770.7(c)(1)(i) requires EPA-approved TPCs to conform to the requirements specified in the ISO/IEC 17065 standard as it pertains to the process used evaluate, approve, and manage certified producers of composite wood products pursuant to TSCA Title VI. For integrated producers of both composite wood panels and non-exempt laminated products that are produced and certified separately, certificates or scope statements issued by an EPA-approved TPC should provide adequate specificity such that document users can reasonably determine whether the scope of certification applies to composite wood panels, non-exempt laminated products certified as hardwood plywood, or both. EPA accepts documentation of third-party certification or NAF/ULEF exemption issued by an EPA-approved TPC, whether such record is in the form of a single document or multiple documents. The TPC is responsible for ensuring that the approach taken to test and certify the manufacturer’s production operation is appropriate to the type(s) of composite wood products being certified and method(s) used in production. Certificates or scope statements issued by the TPC should thus adequately and fully describe the type(s) of composite wood products to which the certification applies, the location(s) where certified products may be made, and other information as specified in ISO/IEC 17065 as is appropriate to the manufacturer’s scope of operations.
No-Added Formaldehyde-Based (NAF) and Ultra Low-Emitting Formaldehyde (ULEF) Resins
1. I am a panel producer whose products are manufactured under an existing NAF or ULEF two-year exemption from the CARB program. Does this also mean that I am exempt from certification under TSCA Title VI?
Yes. If you have been approved for a NAF or ULEF exemption by the CARB program, then you are also exempt from the certification requirements under 40 CFR 770.15, testing requirements under 40 CFR 770.20, and reporting requirements under 40 CFR 770.40(b). Each exemption is valid for two years before requiring re-approval, so long as there are no changes in the panel production operation, process, or resin system as explained in 40 CFR 770.17(f) and (g) (for NAF resins) or 40 CFR 770.18(h) and (i) (for ULEF resins). The panel producer should work with its third-party certifier (TPC) to ensure the exemption is maintained by reapplying to either an EPA TSCA Title VI TPC or CARB, as needed, to continue manufacturing exempt NAF/ULEF products under the final rule.
2. What are the requirements for composite wood products made with NAF-based and ULEF resins to receive reduced testing and third-party certification exemption?
Composite wood products made with resins formulated with NAF or ULEF resins are eligible for less frequent testing, or a two-year exemption from third-party testing and certification.
Composite wood products made with NAF-based resins require at least one test conducted under the supervision of an EPA TSCA Title VI TPC pursuant to test method ASTM E1333-14 or ASTM D6007-14. Test results obtained by ASTM D6007-14 must include a showing of equivalence in accordance with test method ASTM E1333-14. Also required are three months of routine quality control tests, including a showing of correlation to test method ASTM E1333-14 or the equivalent ASTM D6007-14 test method per 40 CFR 770.20(d), totaling not less than five quality control tests.
Composite wood products made with ULEF-based resins, require at least two tests conducted under the supervision of an EPA TSCA Title VI TPC pursuant to test method ASTM E1333-14 or ASTM D6007-14. Test results obtained by ASTM D6007-14 must include a showing of equivalence in accordance with test method ASTM E1333-14. Also required are six months of routine quality control tests, including a showing of correlation to test method ASTM E1333-14 or the equivalent ASTM D6007-14 test method per 40 CFR 770.20(d), totaling not less than ten quality control tests. The TPC number must be included on the required label for composite wood panels meeting the NAF and ULEF requirements. Additionally, panel producers manufacturing NAF and ULEF exempt panels may, but are not required to, label that the composite wood panels were made with NAF and ULEF resins in addition to all other label requirements.
3. Are melamine- and urea-formaldehyde resins considered NAF-based resins?
No. Melamine- and urea-formaldehyde resins are not considered to be NAF-based resins, and producers of composite wood product panels made with either a melamine or urea-formaldehyde resin are not exempt from the testing and certification requirements under the NAF provisions. Soy and polyvinyl acetate (PVA) resins are noted by EPA as being candidates for NAF-based resins and producers of composite wood product panels made with either PVA or soy resin would be considered eligible to apply for the NAF-based resin exemption under 40 CFR 770.17.
4. Beginning June 1, 2018, what records or documentation must be maintained to demonstrate initial and continued eligibility for a NAF or ULEF exemption or reduced testing under the final rule?
The records demonstrating initial and continued eligibility for a NAF or ULEF exemption or reduced testing include:
- Approval for reduced testing from an EPA TSCA Title VI TPC or CARB;
- Amount of resin use reported by volume and weight;
- Production volume reported as square feet per product type;
- Resin trade name, resin manufacturer contact information (name, address, phone number, and email), and resin supplier contact information (name, address, phone number, and email); and
- Any changes in the formulation of the resin.
Records demonstrating the initial exemption eligibility under the final rule or CARB must be kept for as long as the panel producer is producing those exempt products.
5. What are the labeling requirements for NAF or ULEF exempt composite wood panels?
Composite wood panels made with NAF-based or ULEF resins may (but are not required to) be labeled as being manufactured in accordance with the NAF or ULEF exemption/reduced testing provisions. However, a label indicating that the product is TSCA Title VI compliant, in addition to other labeling provisions under 40 CFR 770.45, is still required.
6. What are the labeling requirements for component parts and finished goods made with NAF/ULEF exempt composite wood panels, or a mixture of NAF/ULEF and compliant composite wood panels?
If a fabricator uses NAF or ULEF exempt composite wood panels in their finished goods, then the products must be labeled with a statement that the finished goods are TSCA Title VI compliant. Manufacturers of finished goods and component parts that are NAF or ULEF exempt may also choose to label their products as NAF or ULEF exempt. For finished goods that are partially made with panels produced under the NAF or ULEF exemptions, they may, at the discretion of the fabricator, be labeled “product contains TSCA Title VI products and NAF/ULEF products,” “product contains TSCA Title VI products and NAF products,” or “product contains TSCA Title VI products and ULEF products,” whichever most accurately describes the content of the finished good.
7. How should TPCs review and approve applications for NAF and ULEF applications considering the potential for conflicts of interest, potential for inconsistency among TPC reviews, and the potential for inadvertent misuse of confidential information?
To address these concerns and to avoid any potential conflicts of interest, EPA has specifically listed impartiality requirements in the final rule under 40 CFR §770.7(c)(3) to highlight the impartiality requirements found in ISO/IEC standards incorporated by reference under 40 CFR §770.99. EPA notes that the provisions requiring TPC impartiality are applicable to TPCs reviewing and approving NAF/ULEF exemption applications.
Under the final rule, TPCs must:
- Not be, or have a financial interest in a panel producer, fabricator, laminated product producer, importer, designer, distributor or retailer of composite wood products;
- Ensure that TPC management personnel and TPC personnel involved in the review and certification decision-making process for composite wood products are not involved in activities within the same or a separate legal entity that may compromise the impartiality of its certification decision-making process, such as advocacy or consulting activities;
- Ensure that TPC management personnel and TPC personnel of the same or a separate legal entity involved in activities such as advocacy or consulting are not involved in the management of the certification body, the review, or the certification decisions; and
- Ensure that TPC management personnel and TPC personnel certifying composite wood products sign a conflict-of-interest statement attesting that they will receive no financial benefit from the outcome of certification.
8. How much information should TPCs maintain when it comes to the potential for confidential information such as resin formulation data when approving NAF/ULEF applications?
EPA does not require that specific resin formulation information be included with applications for NAF and ULEF approvals and instead only requires identification of the resin system. TPCs do not necessarily need to know the resin formulation of a resin before it is cured because it does not provide adequate information about how that resin will perform from a formaldehyde emissions standpoint. Formaldehyde emissions are predominantly dependent on production variables associated with the wood composite panel manufacturing process, such as press time, adhesive spread rates, press temperature, etc.
9. How much information should TPCs require for a NAF/ULEF exemption renewal?
EPA only requires one quarterly TPC verification test result for NAF renewals and two for ULEF renewals which demonstrates continued compliance with the reduced formaldehyde emission standards for each product type. The test must be based on products randomly selected and tested by an EPA TSCA Title VI TPC or a TPC laboratory. In the case of approval for ULEF reduced testing conducted by an EPA TSCA Title VI TPC, no periodic reapplication to a TPC is necessary because the panel producer must have ongoing TPC oversight. If CARB approved the ULEF reduced testing, the panel producer must reapply to an EPA TSCA Title VI TPC.
10. How does the inspection frequency affect NAF, ULEF, and reduced testing frequency exemptions?
If a panel producer only produces products that have received a NAF or ULEF exemption from TPC oversight, the panel producer is also exempt from inspections. If a panel producer manufactures any products that haven’t received NAF or ULEF exemptions from TPC oversight, it is subject to quarterly inspections by the TPC. In addition, EPA requires quarterly inspections of panel producers that have received approval for ULEF reduced testing.
11. Which type of testing and certification exemption (or reduced testing) are my products qualified for?
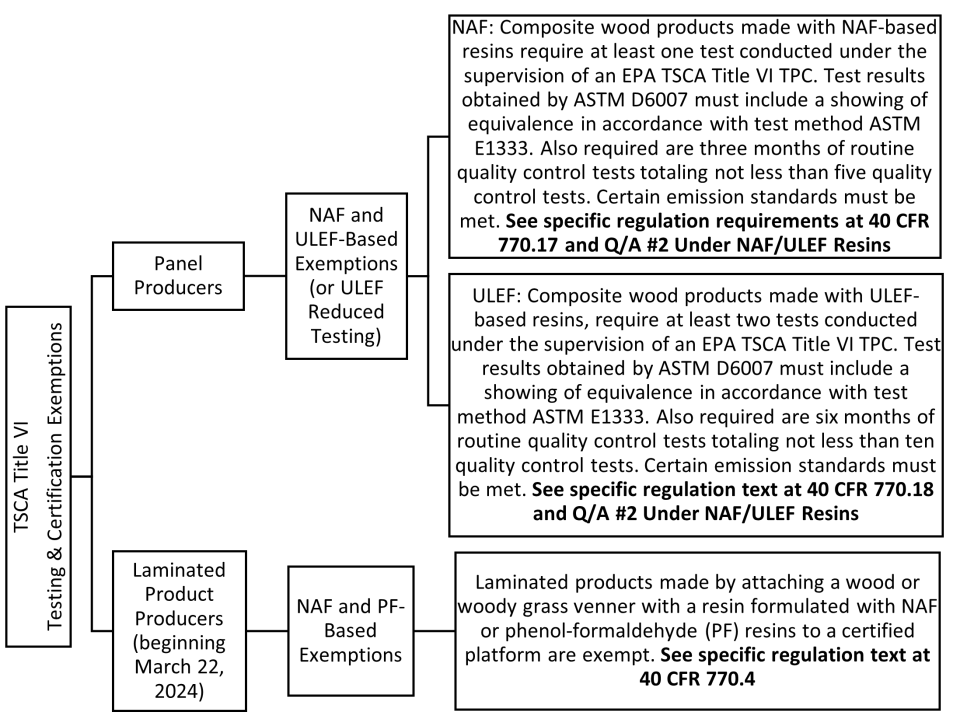
The diagram above outlines the availability of NAF- or ULEF-based exemptions from further testing and certification (or of ULEF-based reduced testing), as well as the additional NAF- or phenol-formaldehyde (PF)-based exemptions for laminated products from the definition of hardwood plywood. Note that other requirements of the TSCA Title VI regulations still apply. For example, for panel-based NAF or ULEF exemptions from testing and certification, please see Q4 in this section for more information on recordkeeping and Q5 and Q6 for more information on labeling. For NAF or PF exemptions for laminated products, please see Q2 and Q3 in the Laminated Products section of the Frequent Questions.
12. If I am a laminated product producer and I don't use a phenol-formaldehyde (PF) or no added formaldehyde-based resin (NAF), beginning on March 22, 2024 can I still apply for ULEF reduced testing?
Yes. Beginning March 22, 2024, laminated product producers whose products are not exempted from the definition of hardwood plywood will be included as producers of hardwood plywood. Therefore, by being included in the definition of hardwood plywood, laminated products also qualify for the exemptions under 40 CFR 770.17 (NAF) and 40 CFR 770.18 (ULEF). While in practice this may be an uncommon scenario given that there are specific exemptions for laminated product producers under 40 CFR 770.4, laminated product producers may also utilize the exemption (or reduced testing) process as hardwood panel producers.
Recordkeeping and Reporting
1. What qualifies as a “comparable” document in the recordkeeping requirement at 40 CFR 770.40?
The final rule gives flexibility to regulated entities with respect to this designation. For most composite wood products commonly bought, sold, or shipped, EPA understands that bills of lading or invoices typically track the product through the supply chain. Packing slips, receipts of transfer and documents “comparable” to these examples may be used to ensure compliance with the recordkeeping provisions of the final rule so long as they bear the identification information for the regulated product. Documents may be maintained in an electronic format (e.g., electronic tracking system, database) so long as all required information under the Toxic Substances Control Act (TSCA) Title VI regulation is able to be generated and presented like a bill of lading or invoice, upon request.
2. Do panel producers, fabricators, importers, and distributors need to put the compliance statement on invoices, bills of lading, and comparable documents, or is placing the statement on one of these documents sufficient?
The final rule allows for flexibility for panel producers, fabricators, importers, or distributors to choose the document on which to include the compliance statement. They may affix the statement to a bill of lading, invoice, or comparable document; all documents; or any combination thereof. EPA only requires that the statement is included on one of the aforementioned documents, is retained for three years, and made available to EPA upon request.
3. Is it necessary to include “TSCA Title VI compliant” on every line item description where it applies, or is a general claim referring to composite wood products being compliant printed on our invoice, bill of lading, or comparable document sufficient?
One description per invoice, bill of lading, or comparable document would be sufficient to adhere to the requirements in the final rule, assuming that statement would be true for all composite wood products on the document. Panel producers or downstream entities may choose to note which products they are certifying on each document if it will promote transparency for downstream entities.
4. I am a panel producer. Am I required to track the composite wood panel bundles to their finished goods?
As a panel producer you are required to maintain records of the purchaser information for each of the composite wood panel bundles you directly sell or distribute. The fabricator and downstream entities are responsible for taking reasonable precautions to maintain a chain of custody for records that identify the supplier of the composite wood products.
5. Am I required to have all records and documents in English?
The TSCA Title VI final rule does not explicitly note that English must be used for invoices, bills of lading, or comparable documents under the recordkeeping requirements at 40 CFR 770.40; however, the final rule does require legible English is used for all TSCA Title VI labels (see 40 CFR 770.45).
The U.S. Customs and Border Protection (CBP) has published a guide titled "Importing into the United States – A Guide for Commercial Importers,” which notes in section 10 that “the invoice and all attachments must be in the English Language, or shall be accompanied by an accurate English translation.” It is also possible that other government agencies have requirements for importing that you should be aware of; the CBP guide above is noted as an example.
6. I am a producer of composite wood panels or non-exempt laminated products that has achieved third party certification by an EPA-approved TPC. Am I required to provide test reports to direct purchasers of these products?
40 CFR 770.40(a) specifies that producers of composite wood panels must make records of all quarterly emissions testing available to direct purchasers of their composite wood products. These records must identify the EPA TSCA Title VI TPC conducting or overseeing the testing. These records must also include the date, the product type tested, the lot number that the tested material represents, the test method used, and the test results. This information may not be withheld from direct purchasers as confidential business information. Other types of test records, including records of ongoing quality control testing, are not required to be made available to direct purchasers of their composite wood products; however certified producers may voluntarily choose to do so.
Beginning March 22, 2024, producers of laminated products are required to test and certify those products as hardwood plywood unless excluded as provided in 40 CFR 770.4. In its definition of the term “laminated product producer” (see 40 CFR 770.3), EPA specifies that “[l]aminated product producers are fabricators and, beginning March 22, 2024, laminated product producers are also hardwood plywood producers except as provided at 40 CFR 770.4.” Therefore, producers of composite wood panels and non-exempt laminated products who are required to achieve and maintain third-party certification must make records of all quarterly emissions testing available upon request to direct purchasers of their composite wood products, including laminated products.
Producers of laminated products made with phenol-formaldehyde resins or resins formulated with no- added formaldehyde as part of the resin cross-linking structure are exempt from the quarterly emissions testing and certification requirements applicable to hardwood plywood producers as provided in 40 CFR 770.4, and thus have no quarterly testing records required to be made available to direct purchasers of their composite wood products.
Labeling
1. What are the composite wood product labeling requirements under the final rule?
Composite wood panels
Each raw composite wood panel must be labeled separately, or a bundle of panels may be labeled. The label can be a stamp, tag, or sticker and must include the panel producer’s name, lot number, the assigned EPA Toxic Substances Control Act (TSCA) Title VI Third-Party Certifier (TPC) number (which, in some instances, may be synonymous with the California Air Resource Board (CARB) TPC number), and statement that the products are TSCA Title VI compliant. If a composite wood panel is not individually labeled, the panel producer, importer, distributor, fabricator, or retailer must have a method (e.g., color-coded edge marking) sufficient to identify the supplier of the panel and linking the information on the label to the products. This information must be made available to potential customers upon request.
Finished goods containing regulated composite wood products
Fabricators of finished goods containing composite wood products must label every finished good or every box or bundle containing finished goods must be labeled. If a finished good (including component parts sold separately) is not individually labeled, the importer, distributor, or retailer must retain a copy of the label, be able to identify the products associated with that label and make the label information available to potential customers upon request. The label may be applied as a stamp, tag, or sticker and must include, at a minimum, the finished good fabricator’s name, the date the finished good was produced (in month/year format), and a statement that the finished goods are TSCA Title VI compliant.
Finished goods, including component parts sold separately to end users, containing only a de minimis amount of regulated composite wood product are excepted from the labeling requirements. A finished good, including component parts sold directly to consumers, contains a de minimis amount of regulated composite wood product if its regulated composite wood product content does not exceed 144 square inches, based on the surface area of its largest face. The exception does not apply to finished goods or component parts that are designed to be used in combination or in multiples to create larger surfaces, finished goods, or component parts.
Composite wood products made with no-added formaldehyde (NAF)-based and ultra-low emitting formaldehyde (ULEF) resins
Manufacturers or fabricators of NAF-based or ULEF resins are not required to but may label products as being made with NAF-based or ULEF resins, in addition to the information required on the labels for composite wood panels or finished goods, as applicable.
Composite wood products not for sale
Panels imported into or transported across the United States for quarterly or quality control testing purposes must be labeled “For TSCA Title VI testing only, not for sale in the United States.” Panels may be re-labeled as TSCA Title VI compliant if test results are below the applicable emission standards.
Does my product require a TSCA Title VI label?
Product Type | Answer |
---|---|
Composite wood panels | Yes. Each raw composite wood panel must be labeled separately, or a bundle of panels may be labeled. |
Finished goods containing regulated composite wood products | Yes. Each finished good or every box or bundle containing finished goods must be labeled (subject to a de minimis exception – see Question 10 under this section). |
Composite wood products made with no-added formaldehyde (NAF)-based and ultra-low emitting formaldehyde (ULEF) resins | Yes (with the typical information). Manufacturers or fabricators of NAF-based or ULEF resins are not required to but may add to the label a statement about the products being made with NAF-based or ULEF resins. |
Composite wood products not for sale | Yes. Panels imported into or transported across the United States for quarterly or quality control testing purposes must be labeled “For TSCA Title VI testing only, not for sale in the United States.” |
Finished goods containing laminated products | Yes. Fabricators of finished goods containing laminated products are required to label finished goods that contain regulated composite wood products (subject to a de minimis exception – see Question 10 under this section). |
Laminated products that are imported, sold, supplied, or offered for sale to a fabricator for further fabrication (beginning March 22, 2024) | Yes. Laminated products are considered hardwood plywood and must follow the same requirements as a panel producer beginning March 22, 2024. |
Other wood products not subject to TSCA Title VI (40 CFR 770.1(c)) | No. Wood products that are not subject to TSCA Title VI by 40 CFR 770.1(c) do not require a label. |
2. Must compliant composite wood products be labeled, and when am I required to begin labeling composite wood products as TSCA Title VI compliant?
Regulated composite wood products, and finished goods containing composite wood products, manufactured in or imported into the United States beginning June 1, 2018 are required to be labeled as CARB Airborne Toxic Control Measures (ATCM) Phase II or TSCA Title VI compliant. All regulated composite wood products, and finished goods containing composite wood products, manufactured in or imported into the United States after March 22, 2019 are required to be labeled as TSCA Title VI compliant.
Until March 22, 2019, CARB ATCM Phase II compliant composite wood panels are considered TSCA Title VI compliant, and the CARB ATCM Phase II label will satisfy the TSCA Title VI labeling requirement. All composite wood panels manufactured in or imported into the United States after March 22, 2019 must be TSCA Title VI compliant and the label on composite wood panels must include the panel producer’s name, lot number, an EPA-recognized TSCA Title VI TPC number, and a TSCA Title VI compliance statement.
Until March 22, 2019, the CARB ATCM Phase II label on finished goods will satisfy the TSCA Title VI labeling requirements. The labels on finished goods fabricated in or imported into the United States after March 22, 2019 must include the fabricator’s name, the date the finished good was produced (in month/year format), and a TSCA Title VI compliance statement.
3. If a component part or finished good that contains regulated composite wood is made on or after June 1, 2018, can I label it as TSCA Title VI compliant even if I used composite wood panels that were produced prior to June 1, 2018?
Composite wood panels produced in or imported into the United States before June 1, 2018 are not regulated under the final rule and may be used in making component parts and finished goods until their stock is depleted (assuming that stockpiling has not taken place in an attempt to circumvent the final rule requirements). Panel producers and downstream entities must keep records documenting that the composite wood panels were manufactured prior to June 1, 2018 for the same three-year retention cycle as required for records of regulated panels. Note however that, beginning August 25, 2017, entities were able to voluntarily label finished goods and component parts as TSCA Title VI compliant if they are made using composite wood panels certified as TSCA Title VI compliant by an EPA-recognized TPC. Fabricators may not use composite wood product stock that was manufactured (including imported) on or after June 1, 2018 which has not been certified by an EPA-recognized TPC as compliant with CARB ATCM Phase II (until March 22, 2019) or TSCA Title VI.
4. Who is responsible for labeling individual composite wood panels when a bundle is opened?
Panel producers and fabricators have the primary responsibility for labeling composite wood panels as indicated by 40 CFR 770.45(a) and (c). If a composite wood panel is not individually labeled, then the panel producer, importer, distributor, fabricator, or retailer must have a method (e.g., color-coded edge marking) sufficient to identify the supplier of the panel and linking the information on the label to the products.
5. Beginning June 1, 2018, do I need to include both a CARB and EPA label on compliant composite wood products and/or finished goods?
Until March 22, 2019, regulated products certified as compliant with the CARB ATCM Phase II emission standards must be labeled as compliant with either the TSCA Title VI or the CARB ATCM Phase II emission standards. Regulated products manufactured in or imported into the United States after March 22, 2019 may not rely on the CARB reciprocity of 40 CFR 770.15(e) and must be certified and labeled as TSCA Title VI compliant by an EPA TSCA Title VI TPC with all of the required accreditations.
6. Do laminated products need to include a label?
Fabricators of finished goods containing laminated products must comply with the rule requirements for fabricators. As fabricators, requirements for laminated product producers include taking reasonable precautions for compliance (40 CFR 770.30), maintaining records (40 CFR 770.40(d)), and labeling finished goods that contain regulated composite wood products accordingly (40 CFR 770.45). Beginning March 22, 2024, laminated products are considered hardwood plywood and must follow the same requirements as a panel producer under 40 CFR Part 770, Subpart C, which for labeling means that laminated products that are imported, sold, supplied, or offered for sale to a fabricator for further fabrication must be labeled as hardwood plywood. Each finished good or every box or bundle containing finished goods must be labeled.
7. What are the labeling requirements for laminated products? Are the requirements different for laminated products that have been incorporated into a finished good vs laminated products that have not yet been incorporated into a finished good?
Laminated product producers are also fabricators and, beginning June 1, 2018, all laminated product producers must comply with the rule requirements for fabricators. As fabricators, laminated product producers are required to label finished goods that contain regulated composite wood products they produce or every box or bundle containing finished goods. If a finished good (including component parts sold separately to end users) is not individually labeled, the importer, distributor, or retailer must retain a copy of the label, be able to identify the products associated with that label and make the label information available to potential customers upon request.
Beginning March 22, 2024, producers of laminated products not exempt from the definition of hardwood plywood will also become regulated as hardwood plywood producers and will be responsible for the same labeling requirements as a panel producer of hardwood plywood when laminated products are imported, sold, supplied, or offered for sale to a fabricator for further fabrication. These products should be labeled according to the requirements for panel producers as provided in 40 CFR 770.45(a). Panels or bundles of panels that are imported, sold, supplied, or offered for sale in the United States must be labeled with the panel producer's name, the lot number, the number of the EPA TSCA Title VI TPC, and a statement that the products are TSCA Title VI certified. If a composite wood panel is not individually labeled, the panel producer, importer, distributor, fabricator, or retailer must have a method (e.g., color-coded edge marking) sufficient to identify the supplier of the panel and linking the information on the label to the products. This information must be made available to potential customers upon request. The label may be applied as a stamp, tag, or sticker.
Exempt laminated products made with phenol-formaldehyde resins or resins formulated with no-added formaldehyde as part of the resin cross-linking structure must be labeled according to the requirements for fabricators of finished goods as provided in 40 CFR 770.45(c).
8. Are labeled goods allowed to use the EPA logo?
No. EPA’s logo may not be used on any label or official certificate. EPA is impartial to the products that are produced under TSCA Title VI and the Agency must not give the impression that EPA is endorsing certain products.
9. Can my label include a barcode?
No. The final rule prohibits the use of barcodes, or non-text labels, as the sole label. The use of barcodes and other machine-readable labels inhibit transparency. Even if the barcode was a universal open system, all entities along the supply chain may not have access to barcode readers or smartphones that can read Quick Response Codes. This would create a technology barrier in accessing this information and could deter retailers from checking the information on labels to ensure it conforms to the information provided to them by their supplier. Likewise, barcodes would be a barrier for some retail customers. Thus, entities that wish to use barcodes must also have the TSCA Title VI required information that is encoded also printed on the label in English text.
10. How do I calculate the area of the finished good I am fabricating to determine if it meets the de minimis exemption for labeling?
The 144-square-inch threshold requirement in 40 CFR 770.45(e) is intended to be calculated in aggregate such that you would sum the area of each regulated composite wood product’s largest surface face contained in the component part or finished good.
In the preamble to the final rule, EPA explained the example of a picture frame: “a frame for an eight-inch by ten-inch picture is made up of two-inch wide and one-inch-thick composite wood product strips. The outer dimensions of the frame would be 14-inches by 12-inches and the inner dimensions would be 10-inches by 8-inches. This frame contains 88 square inches of composite wood product and would qualify for the de minimis exception ([12 × 14] − [10 × 8]).” Note that each of the four composite wood products in the picture frame has its largest surface face added to the largest surface face of the other composite wood products in the frame to aggregate to the total of 88 square inches. In other words, imagine that the picture frame consists of two 12-inch by 2-inch pieces of composite wood products and two 10-inch by 2-inch pieces of composite wood panels to form the complete 14-inch by 12-inch frame. The 88 square inch total is calculated by summing the largest face of each of the four pieces: (12” x 2”) + (12” x 2”) + (10” x 2”) + (10” x 2”). Thus, you would calculate the aggregate area of the largest surface face of each composite wood product face in a finished good to determine if the fabricated product is exempt from labeling under the de minimis labeling provision.
Another example of how to consider surface area of each face in the aggregate might be best demonstrated by a finished good such as a child’s dollhouse. The fabricator would look at the largest surface face of each composite wood product in the dollhouse (e.g., exterior walls, interior walls, floors, ceilings, etc.) and add up the largest surface face of each composite wood product throughout the dollhouse to determine the aggregate surface area for purposes of the de minimis calculation. Another way to look at this example is to visualize deconstructing the dollhouse. Lay all the parts flat on a table and measure the surface area of the largest face of each doll house part that contains regulated composite wood product, and then add them all together to determine if the aggregate sum exceeds 144 square inches. This same approach would be used to determine the total amount of composite wood product in a box.
Importing
1. Are imported composite wood products subject to TSCA section 13 import certification requirements?
Yes. Beginning March 22, 2019, importers of articles that are regulated composite wood products, or articles that contain regulated composite wood products, must comply with the import certification regulations for “Chemical Substances in Bulk and as Part of Mixtures and Articles,” as found at 19 CFR 12.118 through 12.127, or as later promulgated.
2. Under the final rule, is the manufacture-by date for importers the date the composite wood product, component part or finished good was made in the panel mill or fabricator facility or the date it was imported into the United States? Also, does the label on the composite wood product need to reflect the date the product was made or the import entry date?
In the case of imported products, for the purposes of determining the “manufactured-by date,” and ensuring compliance with the rule requirements, the term “manufacture” means the date of import into the customs territory of the United States. However, the label on the imported, finished good must include the date (in month/year format) the finished good is produced in the fabricator facility outside of the United States.
3. What does the manufactured-by date mean for non-domestic producers?
In the case of non-domestic producers, the manufactured-by date is the import-by date, which is June 1, 2018. Beginning on this date, all composite wood panels, component parts, or finished goods containing regulated composite wood imported into the United States must meet the emissions standards, testing, labeling and record keeping requirements of the rule and be labeled as CARB ATCM Phase II or TSCA Title VI compliant. Beginning March 22, 2019, in addition to being certified as TSCA Title VI compliant, all imported composite wood panels, component parts, or finished goods containing regulated composite wood must comply with the TSCA section 13 import certification regulations.
4. For importing Title VI products, what are the TSCA section 13 import certification requirements and what is a positive certification statement?
Imports of chemical substances, mixtures or articles that contain a chemical substance or mixture must comply with TSCA in order to enter the United States. Importers must certify that imported chemicals either comply with TSCA (positive certification) or, if not otherwise clearly identified as a chemical excluded from TSCA, are not subject to TSCA (negative certification). The requirements are described in section 13 of TSCA (15 U.S.C. 2612) and in implementing regulations developed by the U.S. Customs and Border Protection (CBP), in consultation with EPA, at 19 CFR 12.118 through 12.127. In addition, EPA has a companion policy statement on chemical imports at 40 CFR 707.20.
An example of a positive certification:
"I certify that all chemical substances in this shipment comply with all applicable rules or orders under TSCA and that I am not offering a chemical substance for entry in violation of TSCA or any applicable rule or order thereunder."
A positive certification means that the chemical substance complies with all applicable TSCA regulations, including Title VI.
Stockpiling
1. Beginning June 1, 2018, what are the sell-through provisions for component parts and finished goods that are not certified under Title VI?
As instructed by the statute, to avoid issues with sell-through periods, EPA set a manufactured-by date instead of a sell-by date. Any component parts or finished goods containing composite wood products that were produced in the United States or imported into the customs territory of the United States before the manufactured-by date of June 1, 2018, are not subject to the testing requirements and emission standards and thus are not required to be certified and labeled as TSCA Title VI compliant. These component parts or finished goods can be distributed in commerce until the stock is depleted, so long as they have not been stockpiled in an attempt to circumvent the emission standards. Panel producers, fabricators, importers, distributors and retailers must keep records for at least three years showing that the component parts or finished goods containing composite wood products were manufactured prior to June 1, 2018.
Secondhand Goods
1. Do the requirements of TSCA Title VI apply to second-hand retail stores (e.g., second-hand charity thrift stores or non-profit building supply recycling stores) or discount stores that receive donations from consumers and other businesses and later sell, supply, or offer for sale goods which are regulated composite wood products or finished goods containing composite wood products?
Donations of regulated composite wood products, component parts fabricated using composite wood products, and finished goods fabricated using composite wood products from individuals, groups, or businesses that have previously bought those products and used them for their intended end use applications (e.g., use in a home or office) and later removed them from their end use and donated those same products are not subject to the TSCA Title VI regulation as those products have been previously sold (or supplied) to the end user and would be considered “second-hand” upon donation to the second-hand retailer (see 40 CFR 770.1(c)(1)). However, donations from individuals, groups, or businesses of composite wood products or finished goods containing composite wood products that were previously purchased or supplied for the purpose of resale but that were never actually sold and put into their intended end use (e.g., never previously sold or used) would be regulated under the TSCA Title VI regulation and would not be able to use the exception at 40 CFR 770.1(c)(1) for the donations.
One example of this type of scenario would be an individual, group, or business that purchases a pallet of office furniture fabricated on or after June 1, 2018 containing regulated composite wood products sold, supplied or offered for sale to a distributor, retailer, or consumer either immediately or in the future. In this example the individual, group, or business is unable to sell the stock of office furniture and decides to donate to a second-hand charity thrift store (or other like charity) who can sell the furniture to consumers or otherwise find an end use for the furniture. In this example, the furniture was originally purchased by the donating business for the purposes of resale, and only after that business was unable to sell the stock they offered it for donation to the second-hand thrift store. The TSCA Title VI regulation would apply in this example because the products were never previously sold or supplied to an end user by the donating business and the second-hand thrift store is now offering to sell, supply, or offer for sale those products. The exclusion provision at 40 CFR 770.1(c)(1) would only apply to those donated items from individuals, groups, or businesses that were purchased in good faith for purposes other than resale (e.g., purchasing with the intent of giving the products away to charity for no compensation).
Starting-Up New Mills
1. I am panel producer starting-up a new mill or restarting a mill in the United States. How can I manufacture compliant composite wood products so that I can offer those products as soon as possible for sale, to be supplied, or otherwise distributed in commerce in the United States?
The Agency understands that testing of composite wood products (i.e., panels) that is required of mills and EPA Toxic Substance Control Act Third-party Certifiers (TPCs) prior to TPCs being able to certify panels as meeting the emission standards may take weeks or months for some panel producers and TPCs to obtain through typical testing approaches. Thus, alternative testing approaches that can speed up this process, but that still adhere to the rule’s testing requirements, for new mills starting-up or restarting would be beneficial.
The first step in establishing any testing program would be for the start-up or restarting mill to apply under § 770.15(c) to TPC for certification of their composite wood products. The mill (i.e., panel producer) working with the TPC would normally then establish a certification program using the mill’s quality control test method (under § 770.20(b)) that has been shown to correlate to the ASTM E1333 test chamber or equivalent ASTM D6007 test chamber.
One alternative approach that may result in more quickly obtaining the quality control testing data required under § 770.20(b), would be for the mill, in the absence of a correlation between the mill quality control test under § 770.20(b) and the TPC’s ASTM E1333 test chamber (or equivalent ASTM D6007 test chamber), to acquire (from the EPA-recognized TSCA Title VI TPC or other means) an ASTM D6007 test chamber to use on-site at the mill.
Under this approach, equivalence would be established, according to § 770.20(d), at the mill between the on-site ASTM D6007 test chamber and the TPC’s (or TPC’s contract laboratory’s) ASTM E1333 test chamber. Under this approach, the on-site mill ASTM D6007 test chamber that shows equivalence to the TPC’s ASTM E1333 test chamber according to § 770.20(d) would necessarily show correlation to itself under § 770.20(d)(2) and could therefore be used as a quality control test method without additional correlation testing.
Quality control testing must be conducted according to the schedule for quality control testing at § 770.20(b)(2), or more frequently than that schedule if the TPC and mill choose to do so. If the test result of a composite wood product provides an emission limit exceedance for the product being produced, the mill must report the exceedance to their TPC and manage the lot according to the non-complying lot provisions provided at § 770.22.
Once the TPC has confirmed that the composite wood products being produced by the mill are certified as meeting the emission standard, the mill must adhere to all the panel producer requirements under the final regulation, such as working with their TPC under the testing and certification program, labeling composite wood products, and maintaining records. Please refer to EPA’s other guidance materials on the TSCA Title VI program for more information.
2. If I as the mill establish a testing program using my TPC’s ASTM D6007 test chamber under the optional mill start-up and restart approach outlined in question 1, must the ASTM D6007 test chamber onsite at the mill demonstrate equivalence to the TPC’s (or TPC’s contract laboratory’s) ASTM E1333 test chamber before or after the ASTM D6007 test chamber is relocated to the start-up or restarting mill?
EPA believes that equivalence between the TPC’s (or the TPC’s contract laboratory’s) ASTM E1333 test chamber and an ASTM D6007 test chamber being housed on-site at the start-up or restarting mill should generally be established after the ASTM D6007 test chamber is delivered to the start-up or restarting mill, as this typically represents in EPA’s judgment a significant change in equipment, procedure, or the qualifications of testing personnel. For example, the qualifications of the testing personnel at the mill will often be different than those at the TPC. Also, during shipping, transport, installation, and set-up possible changes may occur with mechanical equipment that would otherwise invalidate the equivalence or correlation if established before shipping. However, a mill may be able to demonstrate that the re-location of equipment would not be expected to result in a significant change in equipment, procedure, or the qualifications of testing personnel, such that it would not be necessary to establish equivalence following the re-location.
3. If I as the mill establish an emissions testing program using my TPC’s ASTM D6007 test chamber under the optional mill start-up and restart approach outlined in question 1, how must I handle lots that exceed the emission standards under TSCA Title VI?
Just as with any mill currently producing lots of regulated composite wood product, any composite wood products that exceed their respective emission limits, as shown through the required quality control testing, must be managed as a non-complying lot, and handled according to the non-complying lot provisions provided at § 770.22.
4. Can I use testing data generated from my equivalent ASTM D6007 test chamber (acquired from the EPA TSCA Title VI TPC or other means), which is housed on-site at my mill for the purposes of the mill start-up or restart, to establish a correlation to my mill quality control test method (see § 770.20(b))?
Yes, after equivalence has been established between the on-site ASTM D6007 test chamber and the TPC’s (or TPC contract laboratory’s) ASTM E1333 chamber, data generated at the mill from the on-site ASTM D6007 test chamber can be used to establish correlation under § 770.20(d) to the panel producer’s quality control test method as provided in § 770.20(b).
5. If the equivalent ASTM D6007 test chamber (acquired from the EPA-recognized TSCA Title VI TPC or other means), which has been housed on-site at the mill for the purposes of the mill start-up or restart testing, is moved back to the TPC laboratory for them to use for the required quarterly testing of panels from the mill, must equivalence be reestablished between that TPC’s ASTM D60007 test chamber and the TPC’s ASTM E1333 test chamber?
As noted in 770.20(d) equivalence should be established whenever there is a significant change in equipment, procedure, or the qualifications of testing personnel. However, a TPC may be able to demonstrate that the re-location of equipment would not be expected to result in a significant change in equipment, procedure, or the qualifications of testing personnel, such that it would not be necessary to establish equivalence following the re-location.
Use of Experimental Product and Resin Systems
1. I am a panel producer that wants to conduct research and development on a new product type. What do I need to do under the rule to conduct this research and development of a new product type?
In the rule, the definition of a panel does not include composite wood products made for the purposes of research and development, provided that these composite wood products made for research and development are not sold, supplied, or offered for sale. Panel producers may therefore conduct research and development activities on such products. Once a panel producer has concluded research and development activities and would like to certify the product as TSCA Title VI complaint so that the products may be sold, supplied, or offered for sale, the panel producer will need to apply to their EPA TSCA Title VI TPC under § 770.15(c), and only after the composite wood products have been tested according to the requirements at § 770.20 and demonstrated that they meet the applicable emission standards under § 770.10, may those panels be sold, supplied, or offered for sale as TSCA Title VI compliant.
2. I am a panel producer who wants to experiment with a new resin system for the purposes of research and development of a new product type. What must I do to begin certifying a new product type, using a new resin system, as TSCA Title VI compliant?
Panel producers can follow the sample testing provisions under § 770.24 which allow for the shipping of composite wood products for the purposes of testing of a new resin system by the panel producer’s TPC for development of a new product type and eventual certification under TSCA Title VI. Once the panel producer applies to their EPA TSCA Title VI TPC for composite wood product certification under § 770.15(c), and only after the composite wood products have been tested according to the requirements at § 770.20 and demonstrated that they meet the applicable emission standards under § 770.10, may those panels be sold, supplied, or offered for sale as TSCA Title VI compliant.
3. I am a panel producer who wants to use a new resin, that is within the same resin system I am already using to make a TSCA Title VI certified product type, for purposes of production (not considered to be research and development) of products that would be offered for sale, to be supplied, or otherwise distributed in commerce. What must I do to continue certifying an existing composite wood product type with a new resin?
The final rule allows for TPCs and panel producers to work together to determine if it is appropriate to combine composite wood products made with a new resin under an existing product type being produced by the panel producer (assuming that resin is part of the same resin system of the previously certified product with similar emission characteristics), or if a new product category needs to be established for certification purposes because of the new resin being used. If a new product category needs to be established, the panel producer and TPC must establish a testing program to ensure the new product meets the certification requirements under the testing provisions at § 770.15(c), which includes generating the required testing data prior to certification and subsequent distribution of the new product in commerce.
4. Are laminated products made with resins that mix NAF and PF resins exempt?
A laminated product made with a resin mixture consisting of NAF and PF resins would be considered exempt from the definition of hardwood plywood under 40 CFR 770.4. The phenol formaldehyde resin is exempt under 770.4(a)(1) and the NAF portion is exempt under 770.4(a)(2).
Suspension and/or Revocation of a Third-Party Certifier's EPA Recognition
1. What happens when a TPC's recognition has been suspended or revoked?
Suspended TPCs may not certify any products under the TSCA Title VI program for the duration of their suspension. Revoked TPCs may not certify any products under the TSCA Title VI program until they have reapplied for recognition and been recognized again under the TSCA Title VI program.
A suspended or revoked TPC must immediately notify all panel producers to which it provides certification services of the suspension or revocation.
The process for suspending or revoking a TPC’s recognition status is outlined under 40 CFR 770.7(e)(3).
2. Why would a TPC's recognition be suspended or revoked?
EPA may suspend, revoke or modify the recognition of a TPC if the TPC:
- Fails to comply with any requirement of TSCA Title VI;
- Makes any false or misleading statements on its application, records, or reports; and/or
- Makes substantial changes to personnel qualifications, procedures, or laboratories that make the TPC or TPC laboratory unable to comply with applicable requirements.
3. How long does suspension last?
Suspension generally lasts for 90 days from the effective date noted in the Suspended or Revoked Third-Party Certifiers (TPCs) under Toxic Substances Control Act (TSCA) Title VI Program list. If a suspended TPC has not taken action(s) to address non-compliance with the TSCA Title VI program by this date, EPA may take action to revoke their recognition under the TSCA Title VI program.
4. I am a panel producer. What should I do if my company obtains certification services from a TPC that has been suspended or revoked?
Affected panel producers using the certification services of a suspended or revoked TPC have 90 days to obtain the services of another EPA-recognized TPC. If the panel producer is not able to obtain the services of another EPA-recognized TPC within 90 days, the panel producer may request a 90-day extension from EPA. During the time the panel producer is seeking a new TPC, it must continue to comply with all other requirements of the TSCA Title VI program, including quality control testing. Affected panel producers may refer to 40 CFR 770.7(f)(2)(i) for more information.
5. Where can I find a list of TPCs whose recognition status has been suspended or revoked?
Read the list of suspended or revoked TPCs under the TSCA Title VI Program online.
Miscellaneous
1. Is it possible for one company to be considered as more than one type of regulated entity (i.e., panel producer, fabricator, laminated product producer, distributor, retailer, and importer)?
Yes. Under Title VI of the Toxic Substances Control Act (TSCA) it is possible for a company to fit into more than one designation of regulated entity. It is important for each business that works with composite wood products to understand their requirements. EPA has prepared several small entity compliance guides to assist with determining designation and requirements under TSCA Title VI. If you are unsure about your designation under TSCA Title VI, please contact EPA online.
2. Will the final rule preempt California Air Resources Board (CARB) program requirements?
The final rule does not preempt the CARB program. CARB and EPA continue to work together to harmonize the two rules as much as practicable. It is important to ensure that you are compliant with the TSCA Title VI federal regulation and the CARB program if you are doing business in California.
3. How does the TSCA Title VI regulation for Formaldehyde Emissions from Composite Wood Products at 40 CFR Part 770 apply to entities that sell, supply, or offer for sale composite wood products and finished goods containing composite wood products in an e-commerce environment?
If an entity sells, supplies, offers for sale, or imports a product regulated under TSCA Title VI (including the regulated panel or the finished good which contains regulated panels), then that entity is required to meet its respective obligations under the TSCA Title VI regulation at 40 CFR Part 770. Any entity who sells, supplies or offers for sale in an e-commerce environment the following regulated products has obligations that coincide with its designation(s) (i.e., distributor, importer, and/or retailer, etc.) under 40 C.F.R. Part 770: composite wood products, items containing component parts fabricated from composite wood, or finished goods fabricated with composite wood products. This list is not exhaustive.
For example, an entity operating an e-commerce website or electronic marketplace has to comply with the regulations for a retailer if that entity acts as a retailer by selling, supplying, or offering for sale directly to consumers composite wood products, component parts, or finished goods containing regulated composite wood products. Additionally, any entity providing services in an e-commerce environment (e.g., third-party fulfillment, distribution, etc.) that meets the definition of distributor or importer of composite wood products, component parts, or finished goods containing regulated composite wood products has obligations for complying with the regulation based on such designation.
EPA has taken enforcement action against entities selling illegal products in an e-commerce marketplace. Find examples of enforcement actions in e-commerce.
4. Are TPCs required to use the standards that are currently Incorporated By Reference (IBR) in the latest Voluntary Consensus Rules, even if newer, more recently published standards are available?
Yes. Currently, TPCs and other regulated entities must follow the standards that are Incorporated By Reference (IBR) in 40 CFR 770.99 even if newer, more recently published standards become available. EPA has published final rules to update several voluntary consensus standards listed at 40 CFR 770.99 and incorporated them by reference in the Formaldehyde Emission Standards for Composite Wood Products rule.