2024 Green Chemistry Challenge Winners
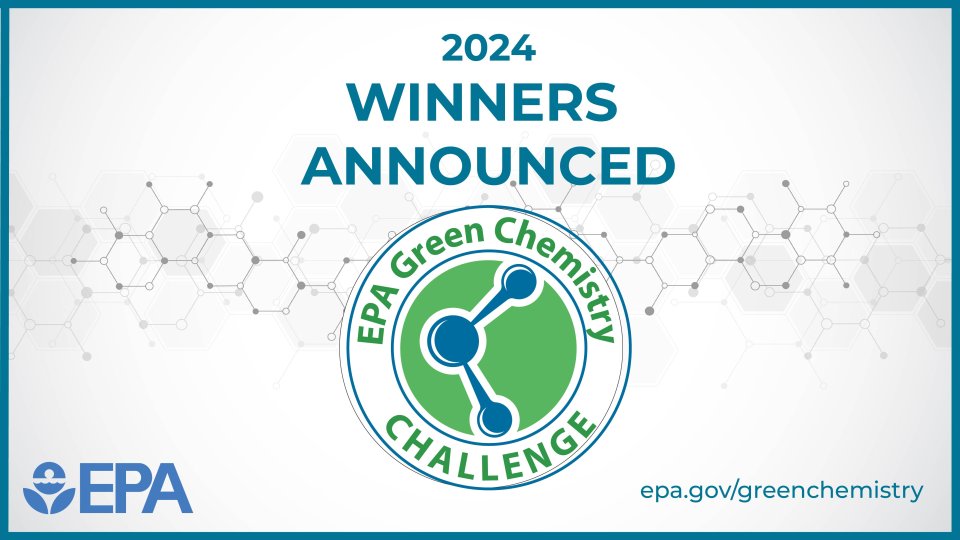
EPA announced the winners of the 2024 Green Chemistry Challenge Awards for new and innovative green chemistry technologies. Through the design of chemical products and processes that reduce or eliminate the generation and use of hazardous substances, this year’s winners have developed solutions to significant environmental challenges such as climate change and spur innovation and economic development. Read the press release.
Disclaimer: Mention of trade names, products, or services does not convey official EPA approval, endorsement, or recommendation.
2024 Greener Synthetic Pathways Award
Merck & Co. Inc.
Merck & Co., Inc. is being recognized for developing a new “continuous process” for manufacturing its PD-1 therapy, KEYTRUDA® (pembrolizumab). Pembrolizumab is an immunotherapy that works by increasing the ability of the body’s immune system to help detect and fight tumor cells. Typically, these types of proteins are produced in large batches. Merck now uses a continuous process to produce pembrolizumab, in which the protein is filtered away from the cells continuously instead of performing a one-time filtration step at the end of a batch. This process can produce substantially more pembrolizumab per reactor volume, which allows Merck to use smaller equipment and thus shrinks the facility’s physical footprint, reducing the facility’s energy use. The continuous process also reduces the energy and water needed, as well as using consumables (such as filters) more efficiently. Reducing the amount of energy and water the facility uses prevents pollution by leading to fewer air emissions.
Summary of Technology
Merck & Co., Inc. is being recognized for developing a new synthesis for its PD-1 therapy, KEYTRUDA® (pembrolizumab). Pembrolizumab is an immunotherapy that works by increasing the ability of the body’s immune system to help detect and fight tumor cells. Typically, these types of proteins are produced in batches from cells that are engineered to produce the desired antibody. Cells are placed in a large vessel where they are allowed to grow for several weeks. The cells and other impurities are then filtered away, leaving the desired protein product. Merck now uses a “continuous process” to produce pembrolizumab, in which the protein is filtered away from the cells continuously instead of performing a one-time filtration step at the end of a batch. The continuous process can produce substantially more pembrolizumab per reactor volume, which allows Merck to use smaller equipment and thus shrinks the facility’s physical footprint. The smaller physical footprint of the facility helps prevent pollution because Merck is able to reduce energy consumption and therefore air emissions.
Merck estimates this continuous manufacturing single-use process reduces energy consumption for Keytruda synthesis by about 4.5-fold; reduces water use by 4-fold; and reduces raw material usage by about 2-fold, thus reducing energy use and greenhouse gases for the facility.
Design of Safer and Degradable Chemicals
Pro Farm Group, a Subsidiary of Bioceres Crop Solutions
Bioceres is being recognized for the development of RinoTec™, an enhanced microbial pesticide for crops including corn, cotton, soy, and wheat. RinoTec is based on a microbe with natural pesticidal effects. Bioceres has engineered the growth of this microbe to produce more of the natural pesticide compound which reduces the application rate for RinoTec. The microbe is grown in large vessels, then killed and incorporated into a seed treatment package that coats the seeds prior to planting. According to Pro Farm Group, RinoTec is “readily biodegradable” and can replace several commonly used synthetic pesticide products.
Summary of Technology
RinoTec is an improvement to their prior product called BIOst®. BIOst is a nematicide and insecticide based on the microbe Burkholeria rinojensis. Unlike BIOst which requires relatively high application rates, for RinoTec, Pro Farm Group engineered the fermentation to increase the production of the key pesticidal metabolite, allowing substantially reduced application rates, thereby reducing the amount of this product being released into the environment. A life cycle assessment by Boundless Impact Research and Analytics scored the BIOst pesticide product a 9.9 out of 10, noting that the Pro Farm Group’s documentation also showed minimal soil, aquatic, and human toxicity as well as minimal ecosystem impacts and harmful materials.
Small Business Award
Viridis Chemical Company
Viridis Chemical Company is being recognized for developing a process for making renewable ethyl acetate, a common chemical that has traditionally relied on fossil fuel feedstocks. Viridis developed a catalyst that allows them to produce ethyl acetate from corn ethanol instead of from chemicals acquired from processing coal or natural gas. The process also produces hydrogen gas as a byproduct, which is used to generate some of the energy needed to operate the plant, thus reducing the plant’s energy needs and therefore greenhouse gas emissions and emissions of other hazardous substances, pollutants, or contaminants associated with energy production.
Summary of Technology
Viridis Chemical Company has developed a synthesis method to produce ethyl acetate from corn bioethanol instead of methanol, the latter of which is typically derived from non-renewable fossil fuel feedstocks. The reaction uses a solid-state catalyst, allowing reclamation of the catalyst constituents at end of life. The dehydration of bioethanol also produces hydrogen gas, which is used to provide about 40 percent of the plant’s energy needs.
Viridis’ process produces high-purity ethyl acetate, which provides a drop-in replacement for fossil fuel-based ethyl acetate. The new process meaningfully reduces environmental impacts compared to the traditional esterification and direct addition routes, scoring better than both methods in most environmental impact categories.
Academic Award
University of Delaware, Professor Dionisios G. Vlachos
Professor Dionisios G. Vlachos is being recognized for developing new synthetic methods to produce lubricant base oils from renewable feedstocks. Lubricant base oils are the main component of lubricants and are used in many applications, including machinery and vehicles. The new technology uses biomass (e.g., plants or food waste) to produce the lubricant base oils instead of traditional petroleum-based materials. The process also eliminates some hazardous reagents, including corrosive acids, used in the traditional synthesis.
Summary of Technology
Lubricant base oils make up about 75-90 percent of commercially formulated lubricants. They represent about a $60 billion market and are used in a variety of applications, such as industrial machinery and vehicles. Traditionally, lubricant base oils have been synthesized from petroleum feedstocks. The new process uses biobased feedstocks, with sugars as the starting point. The new method uses a heterogeneous (i.e., solid) catalyst, which reduces the amount needed and also avoids hard reaction conditions of existing bio-based lubricant production. Professor Vlachos’s team has developed three classes of bio-lubricant base oils with different properties, which they found can provide comparable or better performance to existing technologies.
Specific Environmental Benefit – Climate Change
PhoSul®
PhoSul® is being recognized for developing enhanced phosphate rock fertilizer, which avoids hazards associated with traditional phosphate fertilizer production and improves performance compared to existing rock fertilizers. Phosphate fertilizers improve crop health and yield but need to be in specific forms to be usable by plants. Currently, usable phosphate is produced from phosphorus-containing rock, which must be processed with strong acids, creating a waste (gypsum) that is contaminated with heavy metals and radioactive material from the raw material. PhoSul has developed a method to use phosphate rock directly by enhancing it with other materials, avoiding the need for acid processing and the associated wastes.
Summary of Technology
PhoSul® has developed an enhanced phosphate rock fertilizer, which avoids hazards associated with traditional phosphate fertilizers, while showing significantly better performance than existing phosphate rock fertilizers. PhoSul’s fertilizer consists of spherical granules of phosphate rock with other materials that improve phosphate availability for plants. The additional materials allow the tricalcium phosphate in the phosphate rock, which is not available to plants, to be converted into available forms in the soil. This avoids traditional phosphate processing in chemical plants, where strong acids like sulfuric acid are used to convert the tricalcium phosphate into a usable form. Acid processing generates hazardous gypsum waste, which contains concentrated heavy metals and radionucleides from the phosphate rock and can release fluorine into the atmosphere in fluorine-containing gasses such as hydrofluoric acid. Further, PhoSul minimizes phosphate leaching in the field, eliminating phosphate runoff and its associated ecological damage.