Pollution Prevention (P2) and TRI
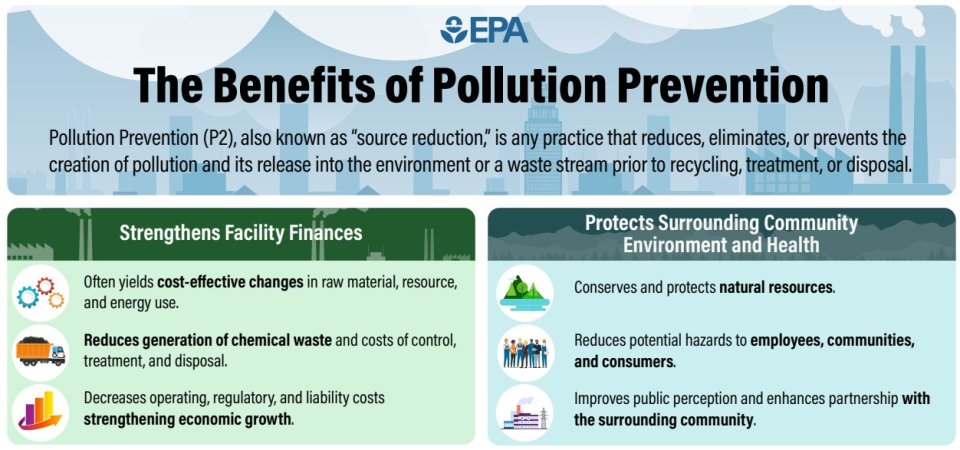
Under the Pollution Prevention Act of 1990 (PPA), the Toxics Release Inventory (TRI) Program collects information to track industry progress in reducing chemical waste generation and moving towards safer waste management alternatives. Many facilities describe measures they have implemented to prevent pollution from chemicals and reduce the amount of chemicals entering the environment. As a result, TRI serves as a tool for identifying effective environmental practices and highlighting pollution prevention successes.
Access TRI's P2 Data
- Use the TRI P2 Search Tool to get info by industry sector, chemical, geography or parent company, and compare environmental performance.
- Use the TRI Toxics Tracker to explore TRI information and quickly filter by industry sector, type of source reduction activity, and other variables.
Learn About TRI P2 Resources
- Browse P2 analyses and publications for information on P2 opportunities and the benefits of implementing P2 at facilities.
- Browse TRI's collection of P2 resources, including factsheets, videos, tips for reporting P2 activities to TRI, and how-to guidance for conducting analyses with the TRI P2 Search Tool.
In 2022, 1,759 facilities (8% of all facilities that reported to TRI) implemented a combined 3,589 new source reduction activities. Process and Equipment Modifications and Operating Practices and Training were the activities reported most frequently. Click on the legend or graph to see examples of source reduction activities; reported codes are included in parentheses.
P2 Examples
- A fabricated metal parts manufacturer purchased new laser cutting machines in 2022 to optimize their process, and in 2022 used them along with water jet cutting machines, which reduced the amount of nickel scrap sent to recycling. (S21)
- A printed circuit assembly facility is phasing out production of products manufactured using a lead bearing wave solder process due to decreased customer demand and transitioning to a lead-free solder or selective solder process. (S23)
- A surgical and medical instrument manufacturing facility optimized the change-out schedule for raw materials resulting in a 40% decrease in ethylene glycol waste transferred off-site for treatment despite a 20% increase in production. (S41)
- A foam product manufacturing facility communicated with its customer base to coordinate demand and group orders when possible, minimizing the amount of diisocyanates-containing waste created during material changeovers. (S42)
- A chemical product and preparation manufacturing facility implemented a new operating system which improved their inventory control process. (S31)
- A plastics material manufacturing facility improved their system by identifying suitable off-specification finished goods to rework into new production batches, reducing the amount of ethylene glycol waste created. (S34)
- An automobile manufacturer changed to a purge solvent with lower volatile organic compound (VOC) content, reducing the amount of methyl isobutyl ketone managed as waste. (S03)
- In 2020, a rubber product manufacturer began testing alternative manufacturing aids to reduce the use of TRI-reportable chemicals. The facility has since eliminated the use of ammonia as a manufacturing aid in a dipping process. (S04)
- In 2022, an inorganic chemical manufacturing facility successfully piloted a formulation without barium compounds and plans to use this new formula in all future production of the product line. (S11)
- A travel security equipment manufacturer worked closely with manufacturing partners to develop an alternative product line that uses a tungsten-based x-ray shielding curtain instead of a lead-containing shielding curtain. (S12)